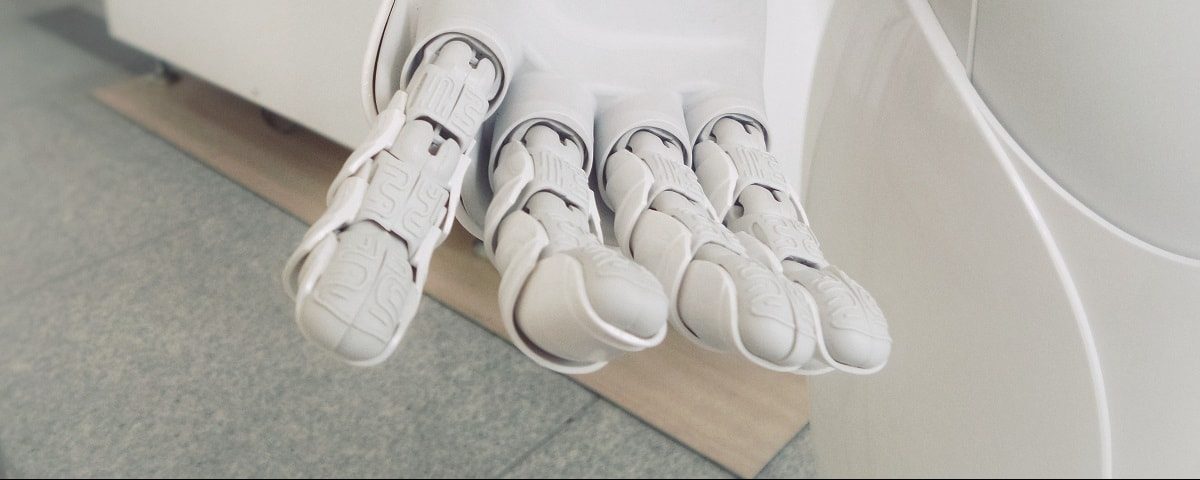
Hoy podemos afirmar que la robótica se ha asentado en el día a día de la gestión de las grandes fábricas e instalaciones: los robots facilitan desde las labores más duras y rutinarias hasta las más peligrosas. Según Deloitte el 94% de las empresas aseguran que la transformación digital es imprescindible, ya que mejora tanto los ratios de productividad como los objetivos operacionales. En el sector de las grandes instalaciones hemos pasado de la gestión analógica a la digital.
La digitalización incluye muy diversas tecnologías para mejorar los procesos que abarcan desde el Internet de las Cosas (IoT), el big data, la automatización de procesos, el uso de la impresión 3D, hasta la realidad virtual. Los ejemplos son múltiples: desde la utilización de robots colaborativos que hacen que el proceso de producción de una fábrica sea mucho más productivo, hasta el uso de la inteligencia artificial para agilizar procesos y corregir errores, así como el uso de la tecnología para reducir la cantidad de residuos y contribuir así al medioambiente. Por ello, muchas empresas han optado por digitalizar la mayor parte de sus procesos e incorporar avances tecnológicos. Con el fin de ahondar en cómo está afectando la tecnología al sector industrial, a sus profesionales y a la gestión de grandes instalaciones destacamos algunos ejemplos de compañías líderes que se están llevando en sectores tan diversos como el aeronáutico, el logístico o automoción. La foto la fijamos en compañías como FORD, Siemens, SEAT o BMW.
TECNOLOGÍA 4.0 PARA OPTIMIZAR LOS PROCESOS INDUSTRIALES
SIEMENS posee, en la ciudad alemana de Amberg, una de las fábricas más tecnológicas y automatizadas del planeta, donde combinan la inteligencia artificial con el análisis de datos para mejorar sus procesos. La planta, especializada en la producción de controles electrónicos programables (PLC) para uso industrial, ha conseguido pasar de gestionar 5.000 procesos de datos al día en 1995 a procesar actualmente más de 50 millones de procesos.
MAVIVA, un referente en el sector logístico en España, ha desarrollado avances en la gestión 4.0 de sus procesos de fabricación, como el robot adaptado para el ensamblaje de parabrisas, que permite obtener unos excelentes niveles de productividad. La compañía cuenta, además, con un laboratorio 3D para realizar controles en busca de la máxima calidad en las piezas.
BMW ha puesto en marcha la integración de información sobre clientes en su proceso de producción. El fabricante de automóviles puso a disposición de sus clientes, entre otros, una plataforma online con la que estos podían personalizar pedidos hasta ocho días hábiles antes de comenzar las tareas de ensamblaje, sin que esto perjudicase los tiempos de entrega.
FORD ha convertido su planta de fabricación en Valencia en una de las primeras a nivel europeo en el sector de la automoción en conseguir reducir a cero el envío de residuos a vertedero. Gracias al uso de la tecnología más innovadora, la compañía fabrica unos 400.000 vehículos al año en esas instalaciones y ha conseguido que la planta valenciana deje de enviar 15.000 toneladas al año de residuos al vertedero.
La fábrica de SEAT en Martorell, Barcelona, cuenta con 125 robots que trabajan de manera automatizada y que transportan casi 24.000 piezas al año por toda la planta de producción. Pueden llevar hasta 1.500 kilogramos de peso y desarrollan sus tareas mano a mano con los trabajadores de la fábrica.
AIRBUS, utiliza la realidad aumentada en las labores de montaje de varios modelos en su planta de Alemania. La propia empresa asegura que, gracias al uso de esta tecnología, han logrado montar los asientos de su modelo A330 seis veces más rápido y reduciendo los errores.
LG Electronics, mediante la implantación del CLOi SuitBot, ha desarrollado los conocidos como robots exoesqueletos que se colocan sobre el trabajador con la misma facilidad de cualquier otra prenda. Gracias a esta tecnología el empleado puede realizar labores con carga de peso reduciendo la presión sobre las piernas y espalda y mejorando su movilidad.
NISSAN, a través de su Innovation Lab en Europa, ha propuesto a diferentes startups un desafío basado en encontrar sistemas tecnológicos inteligentes para ayudar a los trabajadores de sus fábricas a desarrollar su trabajo de una manera más eficiente y productiva. El reto tiene el objetivo de obtener ideas que mejoren la relación entre personas y tecnología en el nuevo entorno digital que afronta la industria del automóvil.
RYSIA trabaja desde hace un año con impresión 3D para la industria naval. La compañía posee tres impresoras 3D industriales que se usan, sobre todo, para producir prototipos de piezas. Las máquinas trabajan en cadena 24 horas al día sacando modelos y produciendo una pieza al día, un proceso que sin estas máquinas tardaría aproximadamente un mes.
Estos son solo algunos ejemplos de lo que hacen empresas punteras en sus sectores. Cada vez son más las empresas que se suben al tren de la Industria 4.0 y, sobre todo, son más las tecnologías que se utilizan para que las empresas sean más productivas, más competitivas y más innovadoras, es decir, para que el sector industrial sea del siglo XXI. Sectores como el automovilístico, la logística, la aeronáutica o la industria naval ya han empezado a instalar importantes avances que le suponen ir un paso por delante en su actividad con respecto a sus competidores, independientemente del sector al que pertenezcan o del tipo de mejora que les suponga invertir en innovación para mejorar sus respectivos negocios. En resumen, la transformación digital ha llegado para quedarse.
Todavía no hay comentarios