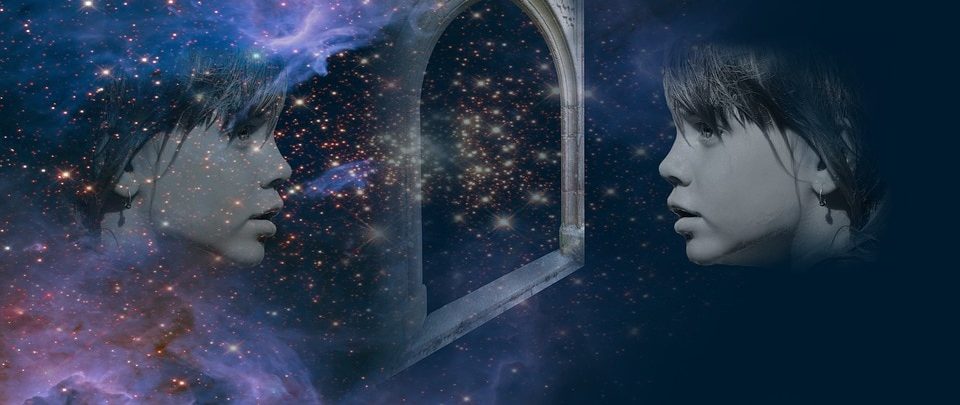
¿Cómo pueden los gemelos virtuales ayudar a optimizar los procesos productivos?
02 de marzo de 2020
El concepto de gemelo digital está a la orden del día y es fácilmente escuchado en cientos de charlas, foros y eventos en los que la Industria 4.0 es la temática fundamental. Igualmente, existen cientos de definiciones y escritos que nos intentan explicar, e incluso vender, qué es un gemelo digital o por qué debe ser la base de la investigación industrial que toda planta de producción debe desarrollar. Sin embargo, las reflexiones aquí descritas tratan de llevarnos al día a día y cómo realmente la utilización de esta tecnología ha permitido mejorar los procesos productivos de manufactura.
Dejando de lado los tecnicismos o las definiciones de la RAE de las palabras «Gemelo» y «Digital», así como si fue la NASA la que acuño el término ya hace unos cuantos años; describiremos en unas pocas palabras el concepto de Gemelo Digital. Concretamente, se trata de una representación virtual e intangible que intenta reproducir una situación física o real como la que se lleva a cabo en un proceso de manufactura. La ayuda fundamental que proporciona el gemelo es la de desacoplar el mundo físico del virtual y que en ese mundo fantástico y lleno de magia sea capaz de trabajar para que en el mundo físico no se produzcan desviaciones no esperadas.
En otras palabras, el gemelo digital tiene que proporcionar una mejora del proceso. En el caso de procesos de manufactura, normalmente, los intereses suelen estar enfocados a la reducción de defectos, mejoras energéticas o las reducciones del time-to-market. Y para ello tiene que hacerlo bajo tres axiomas de funcionamiento claros:
- Proactividad. El sistema debe ser capaz de adelantarse a las situaciones adversas en la producción. Debe hacer uso del mundo digital para que a través de simulaciones e Inteligencia Artificial se pueda determinar la situación en la que se encontrará el proceso productivo en un estado temporal futuro.
- Ajuste. El sistema digital tiene que trabajar siempre dentro de un ajuste específico del proceso de manufactura. De esta forma, todas aquellas simulaciones, pruebas o tests que se desarrollen en el ámbito digital no se escaparán de las reglas que rigen la representación física o real del proceso.
- Inteligencia de negocio. El gemelo se trata de un repositorio global de inteligencia de negocio. Esa inteligencia será utilizada para poder desempeñar sus tareas, pero la importancia es el mantenimiento y gestión de esa inteligencia dentro de la propia planta. Es decir, el gemelo digital, además de ayudarnos en la mejora del proceso, es una herramienta de gestión de conocimiento para la generación y almacenamiento de este.
Toda la teoría es muy bonita, pero la pregunta clave es ¿cómo? Pues la respuesta es sencilla, la forma de conseguirlo es basándose en la metodología que lleva cabo un médico y que recibe el nombre de «Diagnosis». Sus tres pasos básicos: (i) observación, (ii) evaluación y (iii) toma de decisiones.
La observación es la necesidad básica del gemelo digital
La base fundamental de la mejora de un proceso productivo es conocerlo al máximo. Por lo que, además de contar con expertos en ese proceso, es necesario tener una información clara y extensa de lo que acontece en el mismo. Aquí es donde comienza el proceso de observación. Continuando la analogía descrita con anterioridad, los médicos se encargan de realizar una observación a través de sus manos, sus ojos y sus dispositivos de medición. Gracias a ellos recuperan la realidad actual del paciente y eso es la base para su trabajo de diagnosis.
Igualmente, el gemelo digital, trabajando como un médico experto, necesita extraer la información, pero de una forma un poco diferente. Su observación se basa en datos crudos que puedan ser posteriormente analizados a través de técnicas avanzadas de Data Analytics. Estos datos llegan de las comunicaciones que el gemelo tiene con las bases de datos del proceso productivo, la extracción de la información en tiempo real de la red de sensores que hay desplegada a lo largo del proceso productivo (lo que hoy en día recibe el nombre de Internet de las Cosas Industrial) u otros sistemas desplegados en planta para la captura de información asociada a las órdenes de producción, clientes o estados de trabajo, entre otros.
Todos estos datos unidos es lo que va a permitir al sistema virtual trabajar de dos formas claras. La primera de ellas es la primordial y es la base de todo. Es aquella en la que se apoyará el gemelo al completo y es en la que partiendo de esos datos se extraerán los patrones de funcionamiento, las tendencias y otros aspectos que afectan a la segunda de ellas, la predicción o simulaciones de situaciones que podrían darse en el mundo real. También, la observación será útil para permitir trabajar con el estado actual en el que se encuentra el proceso productivo e intentar optimizarlo.
Debemos tener en cuenta que, sin observación, es decir, sin captura de datos, no hay posibilidad de desarrollar este tipo de tecnologías. Es muy probable que lo primero que haya que hacer es abordar algún tipo de proyecto que permita a nuestras plantas avanzar en este nivel. Una vez solucionado esta operación de observación, es el momento de avanzar en el desarrollo de este tipo de soluciones digitales.
Las operaciones que se tienen que realizar serán dependientes de las evaluaciones realizadas
Una vez el gemelo está cargado con el conocimiento generado a partir de la observación de un amplio histórico y el dato actual en tiempo real de lo que está sucediendo en este preciso momento es cuando el gemelo comienza a trabajar. Este proceso es el que se conoce con el nombre de «Evaluación» y es cuando el gemelo digital comienza a hacer diferentes simulaciones con la realidad que está recibiendo a través de la observación. Aquí es donde el gemelo hace usos de las técnicas de predicción y clasificación avanzadas basadas en Inteligencia Artificial con el objetivo de adelantarse a lo que podría suceder en la planta.
Para conseguir llevar a cabo esta tarea de evaluación es necesario desarrollar y combinar diferentes métodos para conseguirlo. De esta forma, en primer lugar, existen simulaciones basadas en métodos clásicos de simulación que hacen el uso de fórmulas que modelan el comportamiento físico en el mundo real. Por otro lugar, existen los métodos basados en el conocimiento experto que ha sido extraído del proceso y de los trabajadores. Esta técnica es una forma sencilla y rápida que hace uso de una serie de reglas y de patrones que permiten obtener esas evaluaciones. Esta técnica se basa en los antiguos sistemas de Inteligencia Artificial que podrían parecer obsoletos, pero que en el caso de los procesos productivos hay ciertas evaluaciones muy sencillas que no necesitan ser complicadas con otro tipo de modelos. Finalmente, existe la posibilidad de hacer uso de técnicas avanzadas de clasificación estadística o clustering. Estas son las que hoy en día están en boca de todos los investigadores y son las que llevan en sus nombres vocablos como Machine Learning, Deep Learning, Redes Neuronales o similares. Aunque pueden ser complicada la forma de generar estos modelos o incluso entenderlos, su objetivo es ser capaces de dar un valor futuro basándose en los casos anteriores y cómo se ha comportado el proceso en esas situaciones. Así, los sistemas hacen uso de diferentes técnicas que permiten representar la información con la que se provee al algoritmo y, finalmente, cuando llega una evidencia nueva (la observación que se ha obtenido en tiempo real) compararla con esos históricos y determinar el estado que se alcanzaría.
Esta etapa es una de las más complejas y la que llama más interés porque es la que se encarga de hacer la magia de los gemelos digitales. Es la etapa en la que el gemelo digital usa su bola de cristal para determinar esas situaciones futuras y adelantarse a la realidad. No obstante, y como bien se había comentado, los modelos que tienen que dar contenido al proceso de evaluación no podrán ser generados sin conocimiento y datos. De esta forma podemos determinar que la observación es la etapa fundamental para que un gemelo digital pueda funcionar correctamente.
Una máquina toma decisiones de optimización del proceso
Una observación por sí sola no va a portar ninguna ventaja al proceso productivo. Es cierto que tendremos un mayor control porque tendremos todo lo que sucede en nuestro proceso registrado y en tiempo real, pero el dato por sí solo no va a mejorar el proceso. Igualmente, el proceso de evaluación es muy interesante, pero saber que vamos a estar en una situación de desviación y que puede generar cientos de problemas en nuestro proceso de manufactura no hace que esa situación desaparezca. Por consiguiente, es necesario que el gemelo sea capaz de realizar la corrección de la situación detectada. Ahí es donde entran los solucionadores o algoritmos de búsqueda avanzados que se encargan de encontrar la mejor combinación de parámetros que hacen evitar la situación detectada.
Para poder llevar a cabo la búsqueda de soluciones hay que hacer uso, de nuevo, de los sistemas de evaluación. Los algoritmos de búsqueda de soluciones tienen que ir trabajando con todas las posibles combinaciones existentes y evaluarlas teniendo en cuenta los posibles estados a los que podría llegar la planta cuando se aplicase esa solución. Estas tareas de cálculo de posibilidades son muy pesadas y gracias a las tecnologías de la información actuales se puede acelerar, permitiendo encontrar la solución más precisa en poco tiempo.
Una vez el sistema ha sido capaz de determinar cuál de esas soluciones es la que mejor se adapta para solucionar el problema, es el momento de generar los mensajes adecuados que hay que transmitir a todos los implicados de la línea de producción. Algunos de esos mensajes podrán ser enviados directamente a la maquinaria y otros de ellos tendrán que ser controlados por los operarios para llevar a cabo las operaciones correctivas. El feedback y la forma de hacerlo dependerá del grado de automatización del proceso productivo. Pero esto debe llevarse a cabo porque sin esta operación correctiva, el proceso no productivo no podrá ser salvado.
En resumen, esta tarea final es la que acaba calculando la solución final y la que propaga el feedback necesario a las máquinas, operarios, dirección, etc. con el objetivo final de evitar los problemas y permitir que, como hiciera un médico, pueda mantener un nuestro proceso productivo sano.
Todavía no hay comentarios