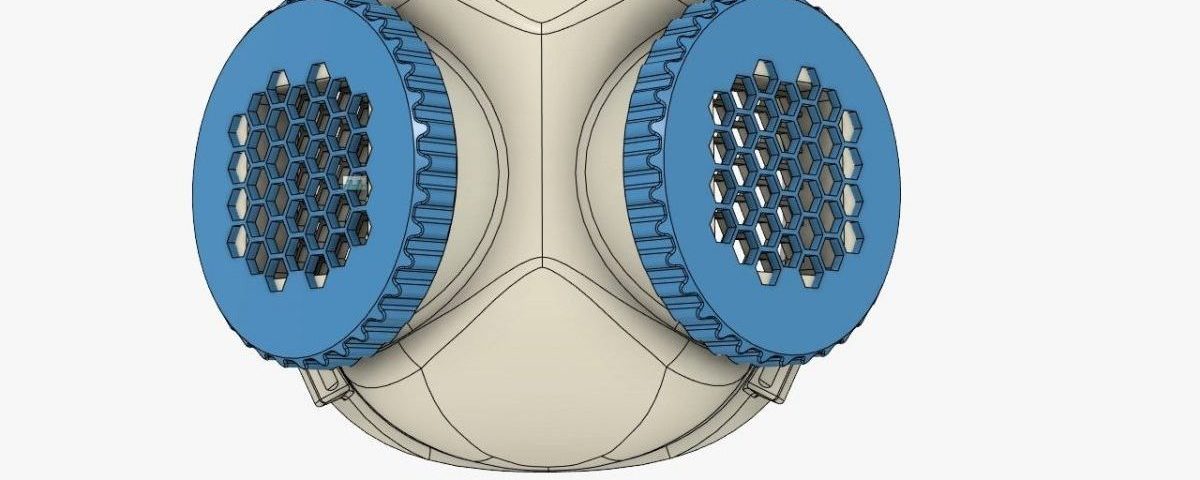
La pandemia de COVID-19 está llevando a los sistemas sanitarios de todos los países al límite de su capacidad. Los hospitales y los centros de salud son la primera línea de acción contra el nuevo coronavirus (SARS-CoV-2) y sus trabajadores redoblan estos días sus esfuerzos para contener la enfermedad. Sin embargo, los materiales con los que estos se protegen, como mascarillas y equipos de protección individual (EPI), escasean.
La demanda de estos equipos se ha disparado en todo el mundo y la industria y el mercado no son siempre capaces de suplirla. Aquí es donde hemos entendido que, desde Ferrovial, teníamos capacidad de acción. Por ello, nos hemos apoyado en la tecnología de impresión 3D para diseñar y desarrollar mascarillas de protección respiratoria esterilizables en los propios hospitales. La fabricación aditiva ha demostrado ser una herramienta eficaz para acortar tiempos de producción y ofrecer alternativas ante la falta de mascarillas.
Una iniciativa para un momento excepcional
La idea partió, en primer lugar, de nuestro equipo de hospitales, los que se encargan de que en los hospitales no se caigan los servicios a nivel mantenimiento y operación, que los servicios sigan vivos en una situación como esta. Desde el equipo de hospitales nos trasladaron sus dudas, preguntándonos si quizá podíamos hacer algo desde el departamento de impresión 3D para desarrollar mascarillas que supliesen la falta de suministro.
Así que nos pusimos a estudiar cuál sería la mejor adaptación de la tecnología de impresión 3D y de qué materiales disponíamos. Ahora mismo existen varios tipos de mascarillas: quirúrgicas, de protección respiratoria y, dentro de estas, de varios niveles de protección (FFP1, FFP2 y FFP3). El objetivo era diseñar una mascarilla para trabajar en entornos de riesgo bajo o medio, equivalente a una FFP2.
De esta manera, dimos con un primer diseño y produjimos un primer prototipo con fabricación aditiva, utilizando tecnología FDM (siglas en inglés de modelado por deposición fundida). Lo fuimos adaptando con varias pruebas y alcanzamos el diseño final. A partir de ese momento, empezamos a buscar un material que fuese esterilizable en autoclave, un dispositivo de esterilización de laboratorio disponible en el propio entorno del hospital, y que no fuese poroso para minimizar el riesgo de contagio a través del material.
Decidimos entonces que lo más sencillo era fabricarlas con nylon P12 a través de la tecnología Multi Jet Fusion (MJF) de HP. Se trata, dicho muy llanamente, de un material en polvo que se solidifica a través de una luz y va generando una estructura en 3D. Y con estos resultados en la mano nos pusimos en contacto con nuestro partner en impresión 3D, Sicnova, que están en Jaén, para que nos imprimiesen las mascarillas.
Un diseño funcional en vías de ser homologado
El material que se usa en entornos hospitalarios sigue un exhaustivo proceso de homologación. La validación y la autorización son fundamentales para emplear las mascarillas impresas en 3D en hospitales, de forma que todo el proceso de innovación sirva para proteger al personal que constituye la primera línea de contención de la pandemia.
En primera instancia estamos imprimiéndolas y testándolas con distintos organismos de cara a su homologación, como el Instituto Nacional de Técnica Aeroespacial (INTA). Lo estamos haciendo así, de forma paralela y simultánea, para intentar conseguir una respuesta lo más rápido posible.
Con la homologación en la mano, no habrá tiempo que perder. Empezaremos a ensamblar las partes de la mascarilla (cuerpo principal, gomas de sujeción y de contacto y filtros) y a repartirlas. Contamos con poder producir unas 3.000 mascarillas cada 10 días.
Flexible, rápido y abierto
Lo más interesante de este proyecto es que el diseño es abierto y lo hemos compartido ya con multitud de empresas en España. Cualquier persona, siguiendo con exactitud el procedimiento que hemos detallado en su dosier correspondiente, podría imprimir estas mascarillas.
La tecnología de fabricación aditiva no solo nos permite compartir con facilidad el procedimiento, sino que nos ha dado la ventaja de la rapidez, algo fundamental en una situación en la que cada segundo es importante. La impresión 3D nos ha permitido tener un modelo final para validar y homologar en un plazo muy corto, algo que en la industria tradicional hubiese tardado varias semanas.
Otros métodos de fabricación tradicionales, como el proceso de inyección, permite producir un mínimo de 2.000 equipos al día, mientras que la impresión 3D tardan cuatro o cinco días en alcanzarse ese volumen. Pero con la tecnología de fabricación aditiva es posible estar fabricando desde el comienzo.
Por último, este proyecto nos ha abierto la puerta de la colaboración con otras empresas de lo más variado, todas unidas para avanzar y buscar soluciones. Moviéndonos para ayudar y aportar nuestro granito de arena en un momento excepcional para todo el planeta.
Todavía no hay comentarios