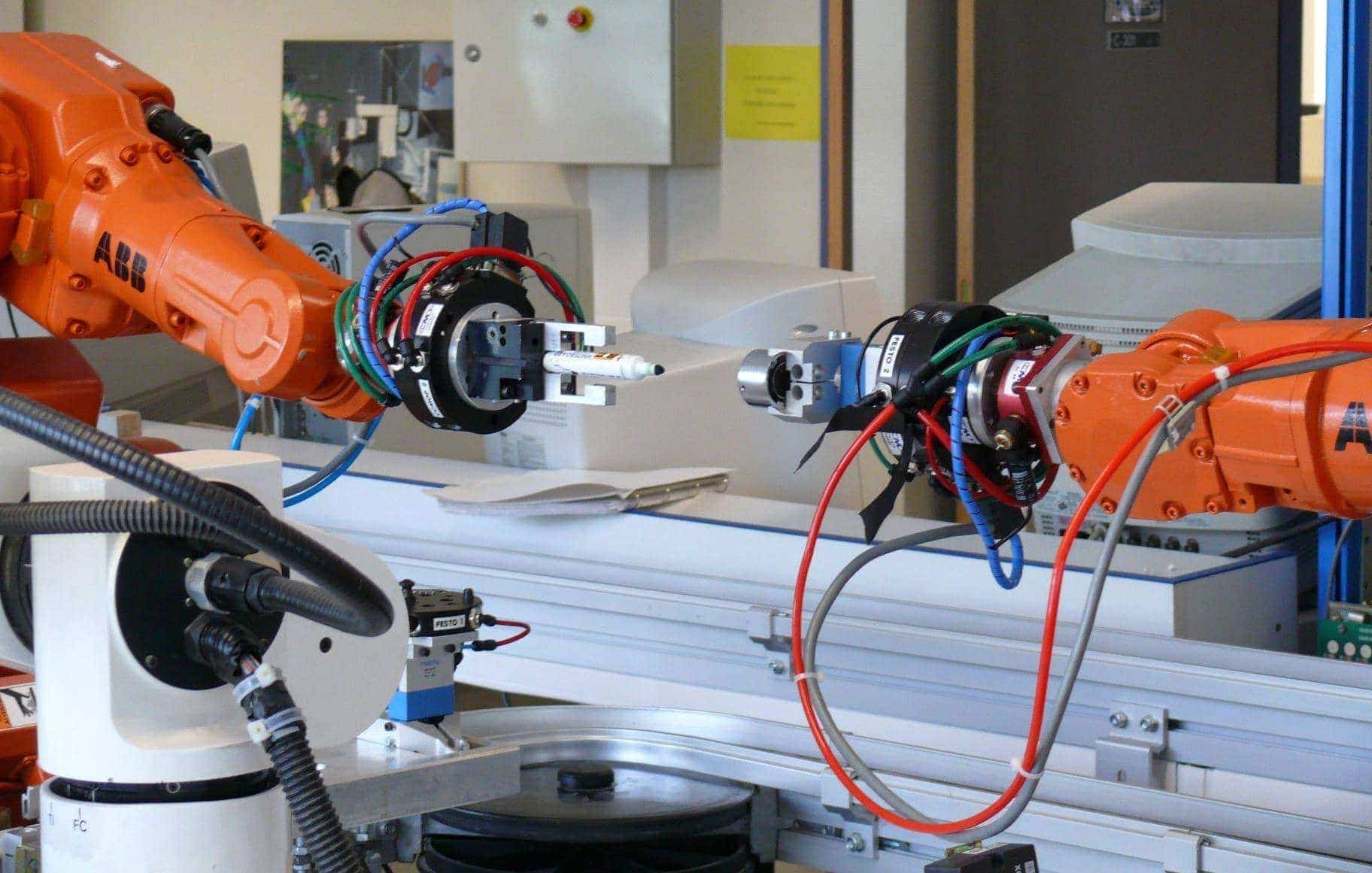
The application of technology in industrial processes has always been a historical trend. Whether talking about the wheel, sails, the steam engine or the combustion engine, technological advances have been part and parcel of industrial progress.
Today, digital technology is everywhere, and its application in industrial processes is giving rise to the fourth industrial generation.
Industry 4.0 has become the argument of choice for companies in critical sectors such as the automotive industry, logistics, transport and energy. One of the reasons for this is the many advantages to be gained from integrating digital methods in industrial processes.
Robots. Photo: Wikipedia
Although the immediate benefits of applying digital technologies in industry are a reduction in operating costs, this is not the sole objective. Digital technology helps to streamline processes, improves worker safety, and widens the scope for research and development.
And digging even deeper to more specific fields of application, certain technologies are a perfect match for industrial processes. This is the case, for example, of companies requiring large infrastructures or transport and communication networks for carrying out their business.
The energy, logistics or transport sectors are a few examples of areas where maintaining infrastructures in good and fully functioning order is a daily challenge, whether it is the locks in the English Channel, high speed railway lines or high voltage electricity pylons.
Costs and safety risks for infrastructure maintenance
Budgets set aside by companies for maintaining infrastructures are sizeable. As examples, maintenance of high-speed railway lines costs Adif around 91,000 Euros per kilometre per year, and around 53,000 Euros for conventional track, down from between 125,000 Euros to 150,000 Euros per km per year for high-speed track and 65,000 Euros for conventional track in 2011.
Considering that Spain has some 2,500 km of high-speed track, these figures are significant and represent a large part of the cost of rail transport, which will eventually be shouldered by users.
Train station. Photo: Manu Arenas
If we look at the water distribution network, Spain has over 155,000 km of pipes for supplying the population. An infrastructure that must be maintained and serviced regularly, giving an idea of the high costs involved.
Another aspect that must be borne in mind when assessing infrastructure maintenance is the human factor. Traditionally, inspection of structures, electricity lines, oil and gas pipelines, roads, etc. has been carried out by specialised staff checking the condition of connection points, ducts, specific structural elements subject to fatigue, or even the vegetation around high-voltage electricity pylons or similar structures.
This type of operation frequently requires the use of cranes, cables or scaffolding for staff to access metres or inspection points, together with sequential, synchronised programming over time, in accordance with the maintenance schedules drawn up by the different companies.
In some situations, these tasks involve risks which must be carefully managed, with stringent safety protocols being followed.
Digital transformation in industrial processes
Digital advances applied to industry have benefited from two trends which have quickly gained momentum over recent months through the consolidation of different technologies. The Internet of Things (IoT), on the one hand, and robotics on the other, with a special emphasis on drones, are opening the door to new strategies for infrastructure management.
Although in fact we should really be talking of three trends if we are to include cloud computing, without which the IoT would not be such a versatile technology. The use of sensors and metres for monitoring the various parameters, which evidence the operational status of infrastructures, is helped greatly if they work through cloud-based platforms.
In a first stage of the move towards Industry 4.0, the most immediate consequence of applying digital processes is a drop in operational costs. But this is all part of a more ambitious process.
“Industrial Internet of Things: Unleashing the Potential of Connected Products and Services”
According to a report by the World Economic Forum, in collaboration with Accenture, “Industrial Internet of Things: Unleashing the Potential of Connected Products and Services” , the process of industrial transformation will go through four phases, the first being an improvement in operational efficiency.
For example, the use of drones is now being tested to inspect high voltage electricity pylons with a view to avoiding damage by the surrounding vegetation. Previously, this was a process which required using a helicopter. A drone costs 6,000 Euros and can be used regularly for structural inspection, whereas a single inspection visit using a helicopter costs around 20,000 Euros taking into account staff, fuel and operational costs in a regular working day.
Using the Internet of Things, sensors can be placed on structures such as the blades of a wind turbine, or on railway lines and power lines, allowing warnings to be received in real time without having to wait until damage or failures are detected by maintenance teams during routine inspection visits.
Human transformation
Together with this digital transformation come changes in the work teams. Where it was previously necessary to climb up onto a platform at a height of 50 metres to see whether a dam had any structural damage or materials fatigue, a drone equipped with a camera can now be used.
Whereas in the past structures such as oil pipelines, pipes, buildings or communications infrastructures had to be visually examined, today it is easy to know whether something is wrong through installed sensors which measure temperature, vibrations, energy consumption, expansion or the presence of dangerous gases, for example.
The immediate consequence for maintenance staff is the need for training in new disciplines, such as piloting of drones, data analysis or applications programming.
Ultimately, applications allow easy interaction with a company’s internal systems on the ground, and as such they must be programmed by the companies so that they can be adapted to their own specific operational processes.
Process transformation
Both digital transformation and human change imply changes in a company’s operational processes. This concept is easier to understand using an example. If a sensor detects a fault in one of the lights of an airport landing strip, a signal is sent to the management platform “on premise” or through the cloud. A fault report is generated, and a member of staff alerted to carry out repairs. The system itself closes the incident once it detects that the light is working again.
Before the advent of the IoT, this process would first require maintenance staff to report the fault. The management system would then generate a repair order, a member of staff would be assigned to carry out the repair, and this staff member would report back once the fault was repaired. The control centre would then close the incident.
All of this can be done using mobile devices equipped with apps tailored specifically to meet the needs of maintenance staff.
A puzzle with myriad pieces
The use of methods and technologies such as the IoT or drones by companies is only the first step in the move towards Industry 4.0. In practice, IoT depends on connectivity, security, and the uptake of other trends in computing such as Big Data, analysis, or data viewing.
Data viewing. Photo: Manu Arenas
Adding connectivity to devices in the IoT comes at a cost of barely five dollars – a cost which will no doubt decrease further –, so it seems financially feasible to use sensors widely. However, connectivity technology, data security and device resilience must be improved.
As for drones, although they seem to be the ultimate universal solution, basically they are no more than a specific type of robot: an autonomous device capable of carrying out certain tasks without the need for a pilot.
Drones are robots that fly; but there are also robots which can move on water or over tracks and roads to identify faults, leaks, breakages or any other incident. Humans are only required for remotely and safely controlling such drones.
We may as yet not have all the pieces to the puzzle, but nonetheless projects are already being implemented on the basis of these trends, having moved on from experimental initiatives.
Innovation is key
For the time being, until standards are set to allow widespread use of the IoT and regular and properly regulated use of drones and robots within industrial applications, what we are seeing is a succession of pilot projects and developments for testing the efficiency and profitability of these systems.
One of the keys to innovation in the digital age is the use of start-up talent: young entrepreneurs who can, thanks to digital technology, develop projects at minimal investment cost using open code platforms or cloud computing.
Large companies, on the other hand, can access these projects through start-up “incubators” or events such as Southsummit where companies and entrepreneurs come together: the former looking for solutions, the latter offering them.
Some examples
A great number of projects have been launched over recent years by large companies such as Ferrovial, Iberdrola, Endesa, Adif, Renfe or Repsol, applying innovation as a means of making more efficient use of existing infrastructures, and of adding value to structures built from scratch.
According to a report from ONVIA, there are several trends providing a competitive advantage in the contracting of public works, one of which is linked to the development of smart infrastructure.
Another of these trends relates to the use of open data, giving an idea of the importance for companies of adopting smart strategies.
Ferrovial Services is one such example of success. Through its Centre of Excellence it was the first company to obtain a licence for flying drones, and is already using them as a tool for exploring work site areas to obtain mapping information and track works progress.
Ferrovial also uses drones (specifically a fixed wing model from Aerotools-UAV) to inspect roads and motorways using image analysis technologies.
This same company, Aerotools-UAV, works with the Spanish power grid company (Red Eléctrica, ree.es) on a project which uses multirotor drones to inspect power lines.
Adif also plans to use drones to inspect its high-speed rail lines, in much the same way as the French rail company SNCF is already doing on some of its high-speed lines.
The University of New Mexico, the San Diego State University and BAE Systems have launched a system for detecting damage after natural disasters such as hurricanes and earthquakes. By comparing images from before and after, the system can detect differences in infrastructures requiring immediate attention.
Power companies such as Iberdrola and Endesa also use drones for inspecting high-voltage power lines, although again these initiatives are still at an early stage.
Leeds, in the north of England, is working on a project which uses robots for monitoring road surfaces, lighting and other elements of city streets so that repairs can be carried out automatically, without the need for human intervention,
Linked to the IoT, Ferrovial has won an enerTIC Award for best innovation project with its “Light for Glass”, which uses Google Glass to facilitate the work of staff carrying out maintenance on road and urban infrastructure through an app which interacts with the Onvia 60 Lighting platform.
Smart Patrimonio (heritage) is yet another initiative based on IoT, where sensors are used to monitor the temperature, humidity or chemical composition of historical buildings making up Spain’s cultural and historical heritage.
Parking solutions. Photo: Manu Arenas
Logistics is yet another area with great potential. IoT is working well for fleet control, and there are already some well-defined and consolidated commercial solutions in operation. For delivery of merchandise and parcels, however, drones are still very much anecdotal stories in the headlines, rather than a tried and tested system for sending and receiving parcels.
Within cities, sensors on the streets are enabling the roll-out of automated parking systems And in the case of road transport, sensors can guarantee lorry drivers a parking spot, so that they need not waste time looking for somewhere to park, and can thus avoid exceeding their legally set travel times.
Innovation that brings the future closer
For the time being, all of these innovative projects come with a large experimental component. But they are all part of a process through which less efficient solutions are discarded, and the best are kept.
Both IoT and robotics have a long way to go before they can meet the safety and resilience standards required for them to be widely deployed in companies or cities. Nevertheless, the projects in which they have been adopted are starting to show benefits, particularly in the reduction of maintenance costs and streamlining of processes.
There are no comments yet