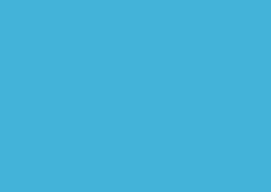
The design and construction of the ITER project is one of the most exciting challenges undertaken by Ferrovial Agroman. As mentioned in a previous post, it’s an environmentally-friendly joint venture by some of the most advanced countries in the world.
The goal is to produce clean energy with no CO2 emissions by means of nuclear fusion, similar to the process that takes place in the sun. The necessary fuel is hydrogen in its two isotopes—deuterium and tritium—which differ from conventional hydrogen in that they have one or two additional neutrons, respectively, in their nucleus. The reaction, occurs when this fuel is heated to form a plasma, i.e. at approximately 100 million degrees Celsius, 10 times the temperature of the sun. For this to occur, an amount of material the size of a postage stamp with a density that is one million times less than that of the atmosphere is introduced into a doughnut-shaped container (toroid), where it is heated and confined by powerful magnetic fields. Once that occurs, the atoms collide and fuse to form stable helium nuclei, giving off a highly energetic neutron. That energy is harnessed in the same way as in conventional power plants, by generating steam to drive a turbine. The main advantage of this energy production system is its safety, since it shuts down automatically in the event of any incident.
However, it will be some years before the ITER complex will be completed, as the first plasma is expected to be produced in 2020. The experimental Tokamak can produce ten times the energy that is input: for example, it produces 500 MW (the output of a medium-sized hydroelectric plant) with just 50 MW of energy to kickstart the process.
In addition to construction, Ferrovial Agroman is responsible for various phases of building design. As could be expected in a project of this type, quality standards are extremely strict, as are the client’s design requirements, which range from general construction organisation to details of the acceleration that would take place in a given plant during a seismic episode. For example, even though the area is rated V on the Richter scale, critical buildings must be designed to withstand a grade IX quake. As a result, seismic dampers have been installed under the Tokamak buildings (contract TB00). These dampers consist of elements that deform under transverse stress and are located on a set of plinths, which enable the building to respond independently from the ground, thereby reducing the impact of a tremor.
It is also necessary to design for accidental stresses, such as explosions and aircraft impact, not to mention fire. Computational fluid dynamics is being used to simulate the temperatures that the structural elements may attain in a number of fire scenarios based on the characteristics and presence of combustible material, the goal being to provide appropriate protection.
The machinery to be housed in the various building merits a chapter of its own, because of the complexities of operating and assembling it. For example, the cryostat, the largest single component of the complex, is so big that it has to be carried by a vehicle as shown in Fig. 6, and its assembly will require two giant gantry cranes, each capable of lifting 1,500 tons, working in perfect synchronisation.
In order to ascertain the presence of any discontinuity in the terrain that might affect the behaviour of the foundation, a tremendous effort is being made to obtain information in the field, including more than 15 km of test drills and hundreds of laboratory tests. The location of each building or facility is investigated in detail, and specific foundation solutions are adopted where needed. To this end, conventional technical studies such as drillings and core sampling are combined with geophysical research using a range of techniques (refraction systems, cross-hole seismic and georadar surveys, and electrical tomography).
The design of the ITER project is the sum of numerous design sub-tasks performed by a plethora of companies from the partner countries. It includes normal features required for an industrial building to function: foundations, structures, walls, partitions, finishes and drainage facilities, utilities, HVAC, electricity, etc. It also encompasses the process facilities, directly linked to each building’s function.
This enormous jigsaw puzzle is being coordinated using CATIA, a CAD program for 3D design, manufacturing and engineering originally created in the aeronautics industry. CATIA integrates all the components into a virtual model representing every detail of the facilities and buildings, including the space reserved for operation and maintenance.
All aspects of the design must match up, so design work is done in real time on the server hosting the full model, either from the central facilities in Cadarache or remotely from the various partners’ design departments.
There are no comments yet