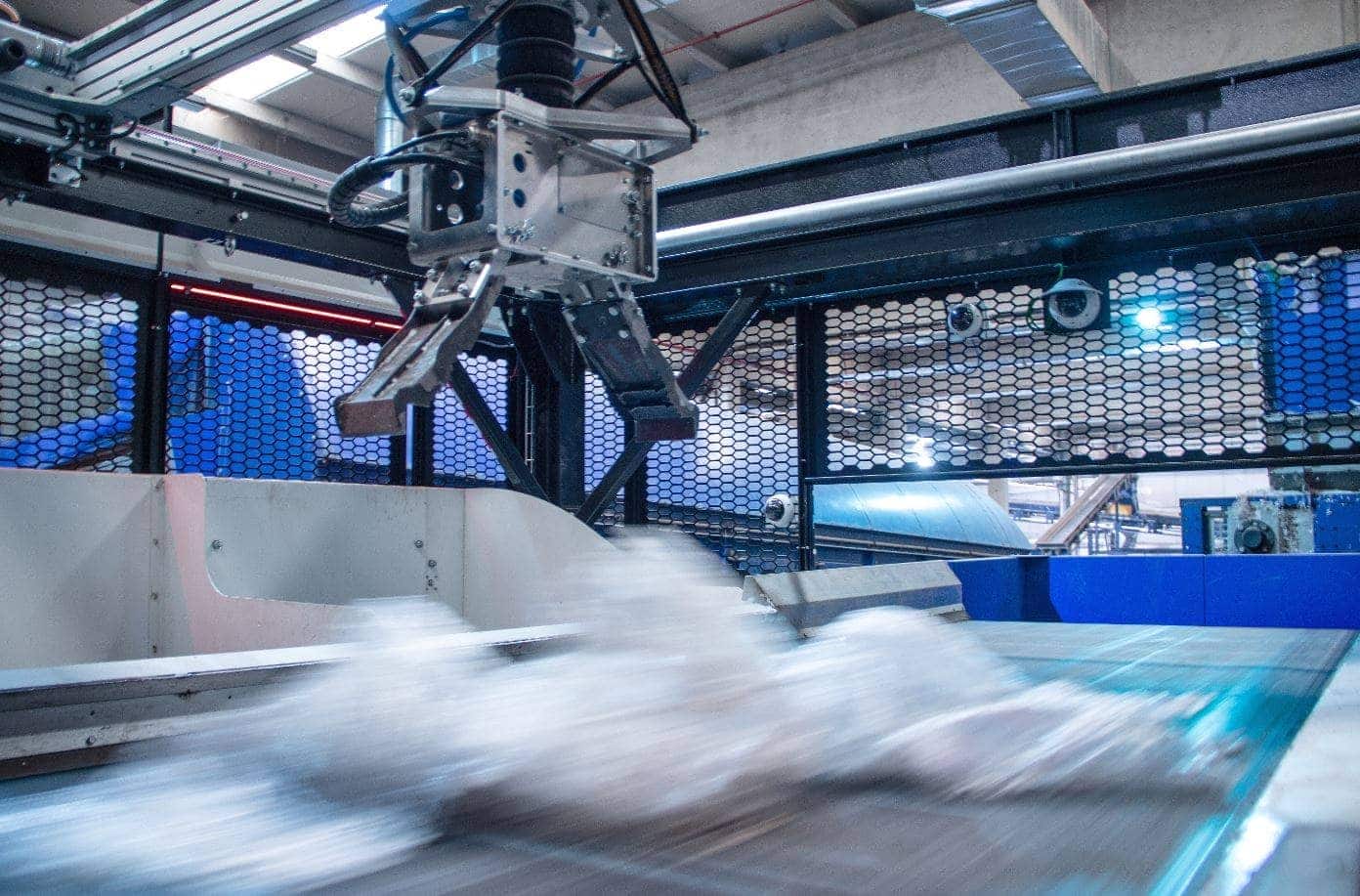
Backup Is on the Way for Separating Urban Solid Waste: A Smart Robot Is Learning
05 of April of 2019
Have you ever asked yourself what percentage of the waste we generate in our homes is recycled? 90%? 80%? Nothing could be further from the truth. The European Commission has set the bar at 55% for 2025, so imagine where we’re at. The data doesn’t lie, there’s still a long way to go. According to Eurostat, in 2016 only 30% of the waste generated in Spain was recycled. The same source estimates that every person in Spain generates about 462 kg of waste per year.
Despite the fact that we are ever more aware of recycling and the importance of separate pick-up, a significant amount of unrecycled mixed waste, called leftover waste, still makes its way to waste plants. However, that leftover waste is a potential source of resources and materials that can be recycled, getting a second life and not ending up in landfills. And that is exactly the goal of applying artificial intelligence and robotics to municipal waste separation, improving the percentages of recovery and recycling by contributing to the circular economy and minimizing what ends up in landfills. Because one man’s trash can be another man’s raw materials.
Manual waste separation: physical, uncomfortable, and highly demanding work
Urban solid waste treatment and separation is a highly automated process. This is a fact. However, there are still parts of the process that are done manually.
This work is done in triage booths, where workers separate waste into categories. This involves direct contact with waste, standing up, and the related discomfort of noises and smells associated with waste. Can you imagine what it’s like to spend 8 hours a day separating trash by hand? It’s a truly uncomfortable job that is physically and mentally exhausting. In addition to the ergonomic problems associated with the physical load and repetitive movements of these tasks, there are other risks linked to this line of work, such as potential blows or cuts from the objects, dropping objects you’re handling, getting trapped in moving objects, coming into contact with chemical substances, biological agents, etc.
For all these reasons, the automation of manual waste separation is expected to help lower the number of accidents and improve working conditions for workers at waste treatment plants, whose jobs could then focus on maintenance of the robots and related devices.
Smart robotics wants to help us… but it still doesn’t know how
It’s clear that the complexity and, above all, the heterogeneity of leftover waste makes automating the separation of valuable materials through traditional methods difficult. But what if we help ourselves with new technologies, like robotics or artificial intelligence? Curiosity around this question has led Ferrovial to sign onto the project “ZRR for municipal waste,” where the first tests will be carried out with a robotic system using artificial intelligence for separating valuable materials from large volumes of leftover municipal waste. The first tests with this smart robot are being carried out at the urban solid waste treatment plant at Ecoparc 4 at Els Hostalets de Pierola, in Barcelona. This is an important and motivating challenge for innovation with a robot called ZRR. With this project, led by Ferrovial and partially financed by Climate-KIC and EIT, right now ZRR is being trained to recognize and separate out 13 types of wastes, including textiles, aluminum cans, polyethylene bottles, cardboard, and transparent film. However, ZRR not only has to separate types of waste, it has to do so fast and well. How fast? About 4,000 picks per hour, which means that each of the system’s two robotic arms has to pick out 1 piece of waste every 2 seconds. How well? The separated waste must have a purity of at least 95%. Even though these are demanding requirements, ZRR has already managed to reach them in its area of specialty, construction and demolition debris (C&DD). And ZRR has been designed, developed, and optimized to separate waste such as wood, big blocks of concrete, and metal scraps. Now, it has to adapt and learn to work in an USW plant, processing waste and materials other than C&DD that is heterogeneous, integrating into a facility with a completely different processing set up than construction debris triage. This process of adaptation is taking time, but the robot is learning!
This is how the smart robot works
The ZRR robot by ZenRobotics can be divided into five parts: the conveyor belt, the recognition sensors, the artificial intelligence software, the robotic arms, and the collection hoppers. Its operations are summed up in the following steps and figure:
1) The ZRR sensor examines the flow of waste.
2,3) The ZenRobotics control software analyzes the information and moves the robotic arms.
4) The robotic arms, two in the case of the Ecoparc4 system, collect the waste from the belt.
5) The robotic arms transport the waste to the collection hopper.
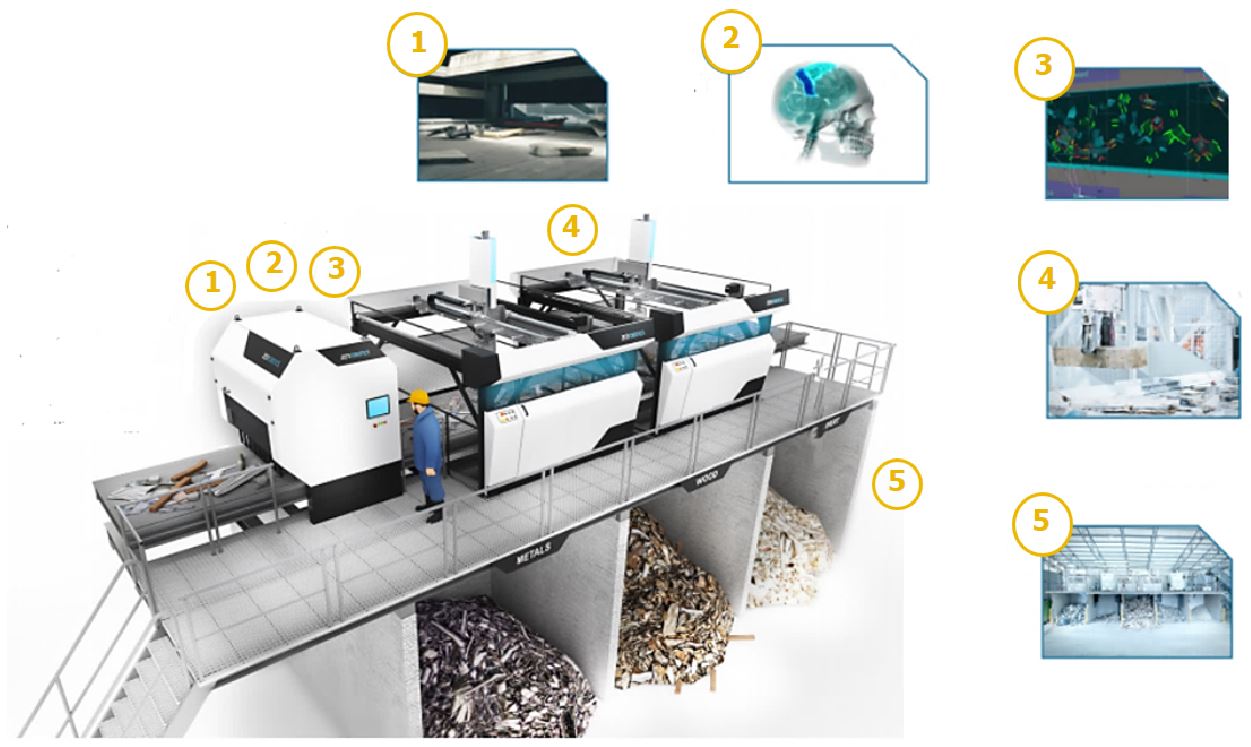
Source: Adapted from ZenRobotics
And that’s how what seems like magic happens, but there’s a lot of science behind it. We must not forget that, like all applications based on artificial intelligence and machine learning, the robot’s operation is based on analyzing input data in order to predict the output results with a lot of help from statistics. In this case, the input data is that of the artificial vision sensors (infrared sensors (NIR), a high-resolution RGB camera, metal detectors, and visible light sensors), and the output results are the classification of waste. Processing the data collected by these artificial vision sensors is what lets the robot classify waste it already recognizes and to learn to classify new waste. And that’s exactly the classification, decision, and learning capabilities that set the ZRR robot apart from other industrial robotic arms; the days of automated sequences of movements that are always the same are over! This robot makes decisions in real time by adapting to the input it has!
In order to physically do the waste separation, the robot has two robotic arms. Each robotic arm is capable of separating up to four different types of waste, which end up in 8 hoppers (four hoppers per robotic arm). In addition, the robot is completely configurable, so the types of waste classified can be selected depending on needs or preferences. Each robotic arm has “pincher” style grip that lets it select different types of waste of different sizes, and it can lift waste of up to 30 kg.
More waste, more training, better results
The ZRR robot and its artificial intelligence software is capable of identifying types of waste, classifying them, and deciding what waste is more important to separate out at each moment. But in order to do this process, it needs training. Every time we want the robot to learn to classify a new type of waste, it needs us to give it reference data: for example, “this is a polypropylene bottle,” or “this is cardboard,” so ZRR can use these examples to learn to classify the different types of waste. Therefore, the operation’s success very much depends on its reference database, so the more reference data it has, and the more types of data, the better the results will be. That’s why one of the main challenges for artificial intelligence is the amount of data required, as well as the time it takes to train and adapt when changing applications or use cases.
Artificial intelligence and automation beyond waste separation
It is expected that artificial intelligence and task automation will revolutionize daily work, and not just for manual waste separation workers, but for many jobs we wouldn’t initially imagine. According to a report published by McKinsey&Company, it is estimated that half of the activities (not positions) carried out by workers could be automated with current technology, even though only 5% of the jobs would be automated completely with the technology currently available. In addition to the benefits associated with improving safety and health conditions for workers, automating some tasks will allow more time and resources to be dedicated to other tasks, and it is expected that new positions will be created that we can’t even currently imagine, as has happened in the past. Additionally, integrating robotic technology will transform current facility design, moving forward in circular economy thanks to the increase in recovery rates and the improvement in quality of the materials recovered, which will help their reintroduction into the value chain as secondary raw materials.
There are no comments yet