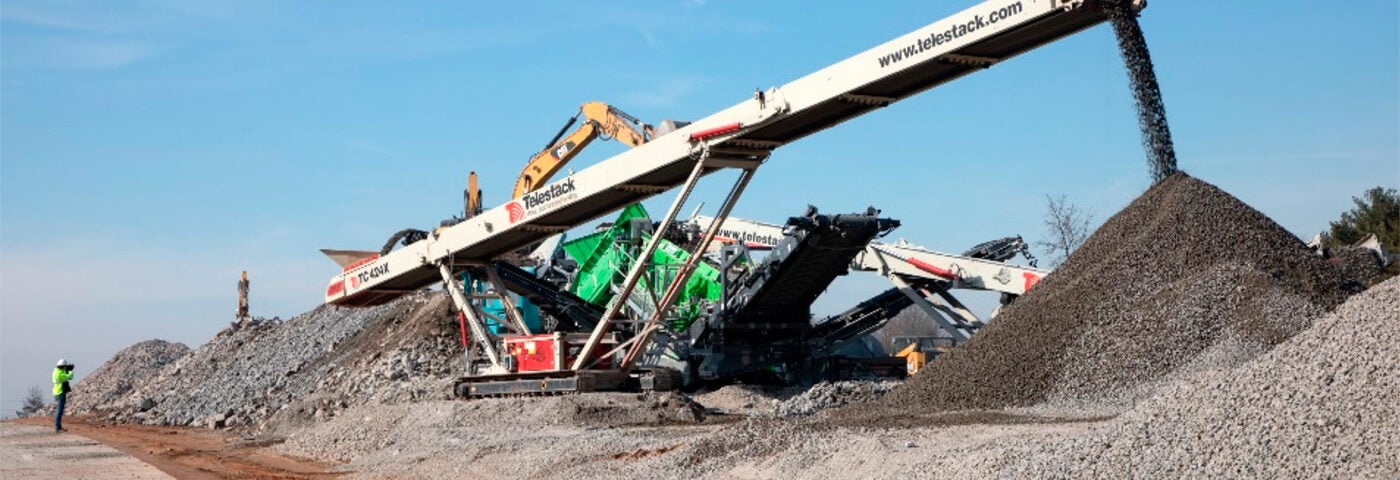
The I-66 Outside the beltway Project is expanding approximately twenty-five miles of the existing I-66 corridor into a multimodal travel solution for the ever-growing northern Virginia region outside Washington, DC. In the densely populated area, the existing roadway configuration wasn’t meeting the demands of the traveling public, so the solution was developed to widen the corridor by adding two new express toll managed lanes alongside three general purpose lanes in each direction, improve and expand bicycle and pedestrian facilities throughout the corridor, construct new park and ride lots to provide new carpool and transit options, and make interchange improvements to enhance safety and reduce congestion throughout the corridor.
To build a new road, you must first remove the existing road to incorporate the design changes and merge it with new roadway. Typically, on a project such as this, the material from the old road would be sent to a landfill for disposal triggering additional impact to the carbon footprint of such massive project. So, the I-66 Project team asked the question “How can we find a more environmentally friendly way of constructing a road?” The answer is a technique known as rubblization.
What Is rubblization?
“Rubble” by definition is “waste or rough fragments of stone, brick, concrete, etc.”
Rubblization is a construction method where the existing concrete pavement is turned into rubble.
When you break apart the concrete and turn it into rubble, you can get a new roadway base that can be simply overlay with new asphalt.
Additionally, whenever the material has to be removed, it eases to take the old road off site more quickly and easily and start building the new one. The downside of a system like this is that it ends up creating a lot of waste to dispose of, creating a negative impact on the environment.
This may sound like a simple solution but rubblization is not as straightforward as it may seem. When you rubblize a road, a special level of care must be taken to ensure that you do not damage the important structural layers underneath. To understand why, we first need to look at the basic structure of a road.
Back to basics: What is under the roadway you drive on?
There are a lot of important structural layers beneath the roadway that lead to understanding the difficulty of the rubblization process. Because rubblization is a solution only for concrete roads, we’re just going to focus on this type of surface.
On the top layer, the surface a vehicle drives one, is a layer of concrete pavement. Below that, is the base course, typically made of a mix of gravel and cement. Below this layer is the subgrade made of well compacted soil, and below that, the existing ground soil. The base and subgrade layers are not as rigid as the concrete structure on top but contribute to the structural capacity of the whole road.
And here is the challenge with rubblization. If not done properly, the rubblization method could damage these vital sub layers, greatly reducing, or completely losing, their structural capacity. Should this happen, a full replacement of all the road layers is needed, making the construction process less efficient and sustainable.
Adding to this dare, in the Northern Virginia area, this technique had never been utilized before and was neither common practice in the rest of the Commonwealth. Until recent technology developments, it’s been quite difficult to safely rubblize a roadway surface without damaging the vital sublayers. When you think about it, you are using a machine that can destroy the surface of the concrete, but you need to make sure that you haven’t damaged the structural integrity of the sub-layers below. It’s a big challenge.
The challenge for I-66
As a technical requirement for the I-66 Project, the Virginia Department of Transportation required that over 1 million square yards of the existing roadway made of concrete pavement be removed and replaced with asphalt. Techniques such as saw cutting or using multiheaded hammers to remove the concrete take considerable time to perform, which adds significant risk to project schedule, can damage the integrity of the sublayers and create significant noise and other environmental concerns in a densely populated area like that of the I-66 corridor.
The I-66 Project team was curious to see if they could use this rubblization technique to overcome this challenge. To determine the feasibility, and to get Virginia Department of Transportation’s (VDOT) approval for using this innovative technique, a series of trials were conducted along the existing road to find out what optimum energy conditions should be applied while using the rubblization equipment, so the underneath layers are not damaged. By doing this, the team was able to come up with an effective construction protocol made ad hoc to determine the appropriate energy exertion for each portion of the roadway that would be broken up.
Rubblizing old concrete pavement on I-66 in northern Virginia
Once the team was able to confirm that rubblization was suitable and gained VDOT approval only as a demolition method, the next interrogation came in: what to do with all the rubblized concrete.
So where does the old road go?
Typically, the rubblized road is transported to a treatment facility where is either dumped and never used again, or the old material is treated, recycled, and reused. In fact, although the treated rubble could become a new base layer for the new road, VDOT original approach for the old road was to have it removed and completely disposed off-site.
Both solutions, whether complete disposal of the rubble and replacing it with material from quarries or trucking the material to treatment plants and bring it back to the site, create another environmental challenge of avoidable additional carbon emissions from the trucking of material off and then back onto the project site.
The I-66 Project team took a further step forward to improve the project sustainability, following an innovative approach to keep the rubblized concrete slab in place when geometrically feasible. By adequately tunning up the rubblizing machinery, the size of the concrete pieces was controlled, ensuring an adequate gradation of the material in place and thus avoiding energy consumption for transportation. As well, mobile crushing operations were set up all along the project corridor, where the rubblized material was broken down into smaller granular pieces.
Once the concrete pavement is turned to rubble, the material is properly seated.
With these both performances a zero-waste scenario is achieved as the old road fully becomes part of the new road one way or another, thus reducing energy consumption and additional natural resources from quarries, and their correlating emissions.
Finally, besides the environmental benefits, reducing the need of off-site trucking in this heavily congested corridor provides a safer place for the daily corridor users.
What are the benefits?
Implementation of rubblizing and processing the material onsite has not only saved time in the construction process, but by avoiding the transportation of the material off and then back onsite, it’s possible to achieve a reduction of 7 million pounds of CO2 emissions compared to a typical offsite processing method.
It is estimated that, by eliminating the need to truck the rubblized material off site for process and then back on site for reuse, over 21,500 truck trips were eliminated, leading to a significant reduction in the carbon footprint being left by the pavement works for this Project.
In addition, by crushing and re-using the existing concrete, the need for subbase material from quarries was reduced by 166,000 cubic yards, which is the equivalent of paving a surface the same size as 100 American football fields. A more efficient use of these natural materials puts a project like this on the path to the ultimate zero waste scenario in the construction sector.
And, as an added benefit, it turns out that leaving the rubblized road on site and using it as a base layer creates an even stronger road than if material from quarries was utilized. The rubblized concrete has a higher strength compared to granular layers of equivalent thickness.
Asphalt concrete placed directly over the seated rubblized concrete
To ensure the quality of the whole product a FWD (Falling weight deflectometer) testing on top of the first lift of asphalt over the rubblized concrete is performed. The final quality is totally assured.
FWD to test strength of pavement layers after first lift of asphalt.
The process is not only more sustainable but also reduces the amount of maintenance needed to repair cracks or other issues on the road in the future.
The road to zero waste
As a result of these innovative efforts made on the, we may see the rubblization process become a common solution on more projects throughout the Unites States in the near future. Rubblization of roadway material is not yet common across the U.S., but as governments look to drive a more sustainable agenda, and the construction industry strives to achieve greater efficiencies, this technique is a way to reduce the environmental impact of road construction while also continuing to offer a high-quality transportation network in a shorter period of time.
In the years to come, engineers may come up with even more advanced techniques to further streamline and improve this process, which surely will lead us towards the goal of building a truly circular construction industry.
There are no comments yet