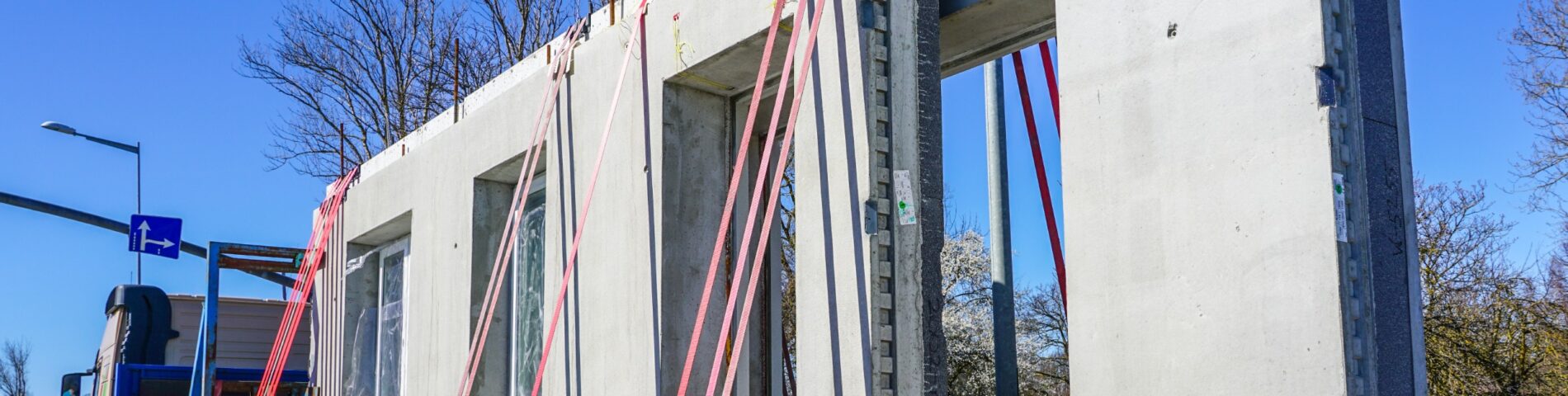
Imagine you have a picnic. You make some sandwiches, some finger-foods, pack the utensils and gear up for a trek into the hills where you find the ideal spot to eat. Compare this with taking all the ingredients and tools with you to the picnic site, then make the meal there. You have to carry the chopping boards, the knives, the packaging etc and then make the food in the hills while bugs attack your, as yet, unfinished sandwiches; it might seem silly.
Now apply this logic to construction sites: Off-site, Modular and Prefab Construction are the equivalent of packing your lunch in advance.
Pros
These new techniques are gaining popularity and it’s not hard to understand why: they offer a number of benefits over traditional on-site construction, including faster completion times, lower costs, and increased safety.
Off-site Construction
Off-site construction refers to any process of building structures in a location other than the final construction site. This can include using prefabricated components, but it can also include using techniques such as panelization, where entire sections of a building are constructed off-site and then transported and assembled at the construction site. This allows builders to take advantage of a controlled environment (in the picnic analogy, this is the equivalent of the kitchen) where quality control is easier to maintain, and the risk of weather-related delays is basically eliminated.
Additionally, it also allows for greater flexibility in terms of design and the use of locally sourced materials; something prized in today’s sustainability circumstances. There is the reduction in delays and sound pollution to the local homes and businesses. Anyone who has lived near a construction site knows how stressful noise pollution can be (and let’s spare a thought for the workers too!).
Modular Construction
Modular construction is a subset of off-site construction, as it refers to the process of building structures in a factory setting (as mentioned above) using pre-fabricated components that are then transported to the construction site and assembled there. Modular construction also specifies the use of standardised components, which can help to reduce costs and speed up the construction process. Additionally modular construction can be temporary or permanent, whereas off-site is typically for permanent structures.
Because the majority of the work is done elsewhere, builders can work on multiple components at the same time, which also reduces the timeline to completion. Work done in a factory setting gives the advantages of economies of scale, further reducing costs.
Prefab Construction
Prefabrication (“prefab”) construction is another branch of offsite manufacturing, where building components are made off-site and then transported to the site of installation to create a structure. In the U.S., prefabrication construction has become increasingly popular in places like Arizona and Los Angeles. This method helps reduce environmental impacts caused by construction projects, such as water-, (the aforesaid) noise-, and air-pollution.
If the difference between prefab and modular eludes you, you are not alone. Often the categories can overlap, but in general prefab is a term that denotes a prefabricated building or building component, manufactured in a factory prior to assembly at a construction site. By contrast modular construction refers to something built or organised in self-contained units—much like bricks or building blocks. A common example of a module or unit would be bathrooms, which are easily modularised.
Safety is also a major benefit of prefab; because the majority of the work is in a controlled environment; this reduces the risk of accidents and injuries on and off of the site.
Sustainability being an ever-present issue, especially in the hotel construction industry, offsite construction has been found to cut greenhouse gas emissions and reduce waste too; these reductions allow developers to be in a better position to meet their sustainability goals and reduce some of the industry’s high carbon footprint.
Cons
Despite the many benefits, there are also some challenges that companies may face when implementing these techniques: One of the biggest challenges is coordinating the delivery and assembly of pre-fabricated components. This can be especially challenging if the transportation and assembly teams are not properly coordinated.
Additionally, there is a risk of damage during transportation which can produce delays across the whole supply chain. Another challenge that builders may also face is the need for specialised equipment and personnel, which are needed to transport and assemble the components.
Lack of flexibility is another factor, as changes in design and plans are impossible once the project begins. This ties quite closely to the lack of customisation of the process. Particularly between regions with differing temperatures and humidities, it is difficult to find one-size-fits-all modules, as materials vary widely in their suitability.
As a result of all the above, extremely detailed planning is necessary to ensure that a project goes well.
Thus, we conclude: Off-site, modular and prefab construction offer building techniques with a number of benefits over traditional methods, but are not without their niches. There will always be room for onsite building, especially in areas with specific needs that are hard for factory planning to anticipate…. Much like spontaneous picnics in unusual locations.
There are no comments yet