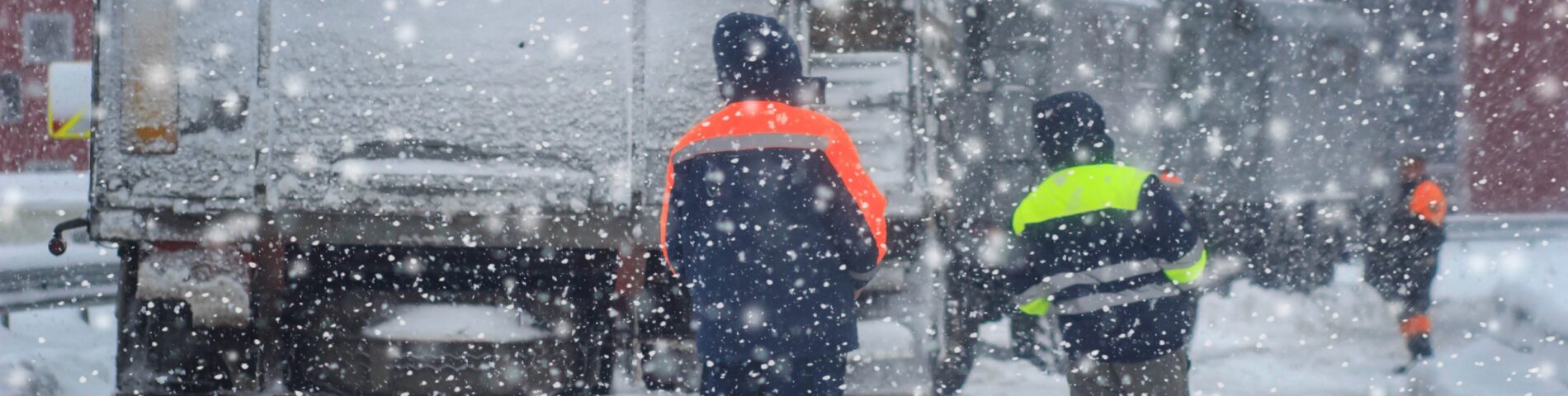
Empowering Employees for Better Health and Safety in Extreme Winters
21 of May of 2024
In places like Canada, winter conditions can be extreme. Temperatures drop, snowfall is common, and it’s not out of the ordinary for Canadians to go about their daily lives wearing ice cleats.
One of the critical operations that keeps people and cities moving safely is road maintenance. Here in the Greater Toronto Area, our teams are in charge of maintaining the 401 Freeway, one of the busiest highways in North America.
After a major snow event, a day on the job could end in frostbite, or even hypothermia, if the proper safety measures aren’t in place. So, how do we keep our workers safe?
When safety comes first, collaboration comes second
People’s Safety is our number one priority. We strive to provide a healthy and safe working environment for all our employees because everybody deserves to go back home safely to their loved ones. Prioritizing safety fosters collaboration, which in turn sparks innovation that ultimately leads to excellence.
And that means we need everyone — laborers, welders, scaffolders, carpenters, plumbers, patrollers, road technicians, leadmen, engineers, and project managers — working together to identify possible hazards and create new preventive and protective measures.
Safety is not one person’s job. It’s everyone’s responsibility.
From the people on the field to the people in the office and up in management positions, we all think about what could go wrong, what could lead to an incident. And then, together, we put measures in place to prevent it.
Overcoming the physical challenges
In the construction as well as industrial sectors, working in extreme winter conditions presents complex physical risks, including:
- Exposure to cold temperatures, which can lead to frostbite, hypothermia, and reduced dexterity.
- Slippery surfaces due to snow and ice, increasing the risk of slips, trips, and falls.
- Limited visibility during snowstorms or blizzards, posing hazards for workers operating machinery or vehicles.
- Potential for accidents involving equipment malfunction or failure due to cold weather conditions.
To overcome these challenges, we focus on PEME: People, Equipment, Material, Environment by:
- Training workers on winter safety protocols and providing appropriate cold-weather gear.
- Conducting thorough risk assessments to identify potential hazards.
- Protecting equipment and materials from frost damage through proper storage and heating methods where necessary.
- Implementing proactive maintenance measures.
- Using materials that can withstand freezing temperatures.
- Clearing snow and ice from construction sites to maintain safe working conditions.
- Continuously monitoring weather forecasts and conditions to adapt our strategies, resources, and schedules accordingly.
- Collaborating closely with local authorities to ensure timely response and support during winter weather events.
However, to have a truly comprehensive and effective health and safety strategy, it’s important to go beyond just the physical challenges.
Keeping employees informed, engaged, and empowered
Maintaining morale is one of the most difficult issues teams face when people are working long hours in cold conditions.
Making people feel valued is one of the contributing factors that help elevate the safety culture. Statistically speaking, employees who feel valued are less likely to commit at-risk behaviors that lead to unsafe conditions and ultimately to accidents.
When employees are well-informed, engaged, and empowered to prioritize safety, they become the first line of defense against potential hazards.
One of the methods we use is continuous awareness campaigns. We ensure that our workers are aware of their rights. In Canada, we have three legal rights: the right to know, the right to participate, and the right to refuse unsafe work. And we provide comprehensive safety training for all our workers. This includes specific seasonal training on physical and mental challenges and the resources that are available to help.
We want workers to get involved and take an active role in improving safety. That’s why we encourage employees to ask questions, make suggestions, and share their thoughts through an initiative called the Yellow Card Program.
Through this program, employees can take a card and write down their thoughts, challenges, or ideas, whether they’re related to health and safety or to some other process in the workplace. They don’t have to write their name, so it’s completely anonymous – No Name, No Blame Culture. And they drop that card into our locked dropbox at the Health and Safety Department.
Every time we receive a yellow card, we create an action item or a business improvement opportunity to follow up. And that’s what makes people feel valued. They know they are being listened to, and they are empowered to speak up and make a difference. That’s the most important thing. Additional actions we take to make employees feel valued include:
- Providing easy access to safety information.
- Establishing clear feedback mechanisms.
- Encouraging participation in safety committees, hazard reporting programs, and safety inspections.
- Involving them in collaborative problem-solving.
- Celebrating safety successes.
A safety-conscious workforce actively identifies risks, reports incidents, and collaborates on safety improvements. When our teams are informed, engaged, and empowered, we create safer and more productive workplaces for everyone.
We prioritize learning, collaboration and safety while acknowledging human imperfection and could make mistakes, fostering problem-solving over blame, and valuing mistakes as learning opportunities.
Welcoming new ideas
A lot of new ideas come out of the Yellow Card Program, thanks to employee contributions.
For instance, we have a joint health and safety committee that’s legally required to meet once every three months. The members of this committee are designated by the union to represent the employees from the field, and we get together to discuss any concerns they have and see how we can help.
One of the suggestions from the yellow cards was hey, why don’t we go above and beyond and hold these meetings once a month? And that’s what we did, starting the following month.
It turned out to be a great idea.
The regular monthly meetings empowered those representatives to be our eyes and ears around the work sites. Once they felt empowered, they started talking to their colleagues, and their colleagues started voicing their own concerns.
This collaboration lets us at the Health and Safety Department know more about what’s going on around the yards and what we can do to prevent an incident or a condition that could lead to incidents. So it’s really made a huge difference.
Innovation and new technologies
Another innovation we’ve seen is the use of proximity sensors. We equip workers with smart wearables and get those devices communicating with sensors inside the machinery operating on-site. If the system detects a potential risk, it alerts the workers. It’s truly revolutionary safety technology.
We’re also thinking about how we might be able to use artificial intelligence (AI) to detect worker fatigue. The idea is in early stages, but it demonstrates that we’re always looking ahead, always curious about new technologies and thinking about how we can make our workers safer.
Shifting the safety mindset
In our approach to human performance, we follow a set of principles that emphasize learning, continuous improvement, and creating conducive environments for safe and effective performance. We recognize the fallibility of humans and prioritize collaboration and problem-solving over assigning blame. Our focus is on harnessing the strengths of our people to drive success.
From the Health and Safety Department, I want everyone to understand that safety is not only about lower incident frequency rates or the absence of accidents.
Safety is about giving people a voice and listening to what they have to say. It’s about collaborating and coming up with new ideas together. It’s about being proactive, not just reactive.
I like to say that in terms of mindset, we’re making a smooth transition from “fix it” to “prevent it.”
And that’s how we go about our daily operations here at Ferrovial.
There are no comments yet