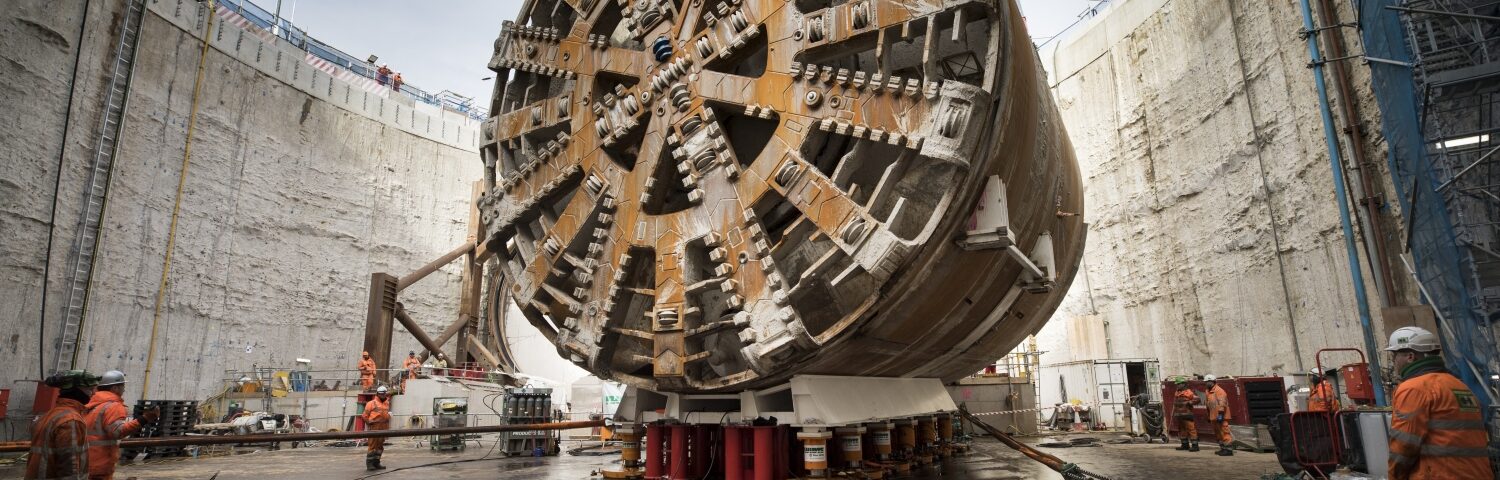
The new 1.4km road tunnel linking Silvertown with the Greenwich peninsula in east London, UK, is the first to be built under the Thames in more than 30 years.
Due to open in 2025, the tunnel will help reduce chronic congestion and allow for better public transport links, including more cross-river bus journeys. The contract is worth more than £1 billion, with design and construction of the project delivered by a joint venture with Ferrovial Construction, BAM Nuttall and SK Ecoplant.
Logistics and engineering on the project have been complex and constrained by many aspects. It is a twin-bore tunnel with a very large diameter, excavated relatively close to the river above, all in a congested industrial area.
Construction under pressure
There are eight cross passages connecting the two tunnels, several of them not far beneath the water, which created an engineering challenge to excavate them safely. Managing the pressure and flow of groundwater, which can sometimes gather in isolated pockets, is unsurprisingly a major hazard in tunneling.
In the tendering phase, we had explored various alternatives to improve the ground around the cross passages, including permeation grouting – the injection of grout material that fills the voids within the grains of soil forming a concrete-like substance – and dewatering, where groundwater is piped out of the earth around the tunnel. In this case, because of the nature and composition of the soil, grouting was not a viable alternative. Dewatering was not feasible due to the size and proximity and of the Thames. It would have required pumping and pumping and pumping again from inside the tunnel.
In the end, having rigorously considered cost, the local geology and all the available technology, Ferrovial made the decision to employ ground freezing for the safest and most solid ground improvement for the Silvertown Tunnel.
Building a tunnel with a big freeze
Ground freezing is an expensive technique where the water bearing strata/soil is frozen to a maximum temperature of minus 10 ℃. Holes were drilled around the cross passages and pipes installed to carry freezing fluid – in this case, brine rather than liquid nitrogen. Over a period of around 40 days, -30℃ fluid was pumped through the pipes by a refrigeration unit, very gradually freezing the earth around it.
During the whole operation, the ground was monitored to ensure there was a solid, frozen cylinder encircling the passage before the excavation could start. It has to be a very controlled environment, where we know the surrounding ground has reached the required temperature. This icy, longitudinal donut-shaped block prevented water from entering the excavation and created a rock-like material which is easier and far safer to excavate.
Ground freezing – which can be carried out cross passage by cross passage in staggered phases along the length of a tunnel – is not a new technique. It is used widely in continental Europe: the Netherlands, Denmark and Germany. But in the UK, it has not been used on many projects and certainly never before by Ferrovial.
Future confidence in ground freezing techniques
We were understandably cautious about this, as it was something new – we devoted quite some time trying to find the right alternative. But after exhaustively ruling out the other options, Ferrovial’s Engineering Services team concluded this technique was right for the specific needs at Silvertown.
Since we didn’t have the in-house expertise or machinery, we subcontracted the specialist German firm Züblin Ground Engineering. We have been extremely impressed by their performance.
The Silvertown project is well advanced and has been very successful. All the tunnels have been bored, the cross passages have been excavated and we are now finalizing building work and road paving.
With the experience we have gained on this project, using ground freezing – when the conditions are right – will be a decision we take with great confidence in future.
Tunnel innovation
Tunneling is destined to become even more prevalent in the infrastructure projects of the future, not least as more and more cities develop underground light railways like the one Ferrovial is working on in Toronto and the proposed metro in Dublin. Especially in urban areas, subterranean work means less disruption, reduced noise and less environmental impact than surface works.
With new tunnel-boring machines (TBMs), better understanding of ground conditions and ground improvement innovations such as ground freezing constantly developing, it is becoming safer, easier and cheaper to build tunnels. Ferrovial is committed to innovation, and making tunneling more productive and cost-effective, safer and more sustainable.
We strive to be at the cutting edge, always gathering experience from our existing tunnel projects, learning lessons to apply in the future. That is a must.
Striving for safe and successful infrastructure
Ferrovial’s Engineering Services team is passionate about projects like Silvertown. It is very important for us to visit sites, to see things safely and successfully become a built reality.
We are not just managers. We like to be very involved in design decisions and very hands on, bringing the experience we have gained all over the world and from Ferrovial projects of the last 50 years into the collaborative infrastructure projects of today.
When people start to use the tunnel next year, most will not be aware of the complex engineering challenges that have been overcome to enable their experience, or the sophisticated solutions that lie just beneath the surface of the Silvertown story.
Riverlinx Ltd, a company comprising Cintra, Aberdeen Standard Investments, BAM PPP, Macquarie Capital and SK Ecoplant – entered into a PPP contract with Transport for London (TfL) to design, build, finance, operate and maintain the Silvertown Tunnel in east London.
There are no comments yet