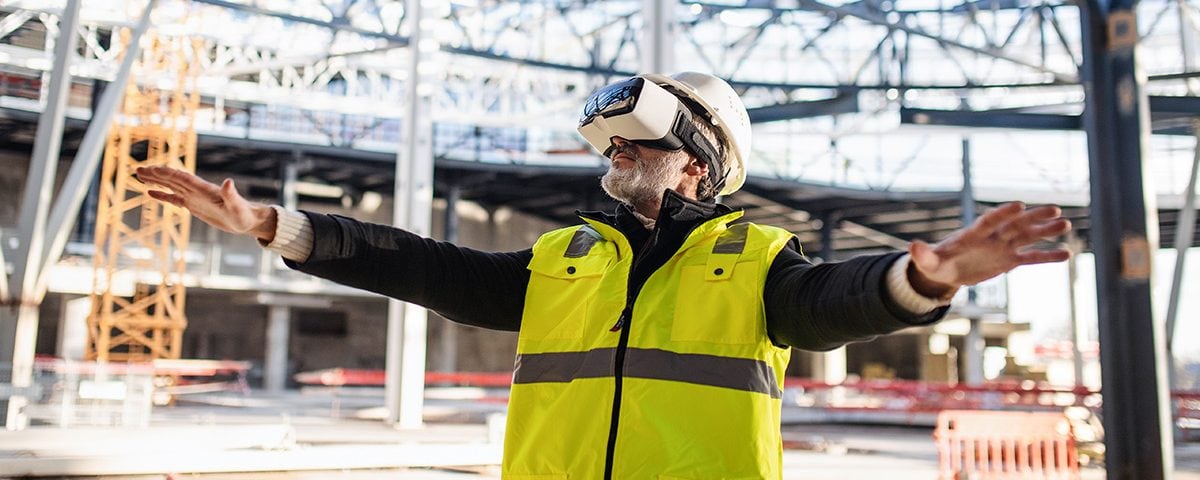
How can new tools and technology can help keep risks under wraps
23 of February of 2022
After more than 20 years of working in H & S – and a decade working in the construction industry alone – I studied for a PhD around safety management and the future role of a safety professional within an organisation.
These roles had often become very administrative in nature, instead of focusing on foresight and future risks. Filling in paperwork about what happened last week is not as valuable as understanding what will need to be managed proactively in the coming days.
Thinking around this is still evolving, but that is the fundamental shift that needs to happen.
When I go into an organisation, I ask about their safety practices and challenge them to say what they are doing now that they were not doing in the 1990s. Most companies struggle to find anything new – H & S is a function that has seen very little innovation for 25 years.
In that time, in many countries, rates of industrial fatalities have been flat or in some cases increasing. Our safety practices, tools and techniques have not kept up with the mounting risk in our operations.
Some firms still base safety management practices on work as it was 30-50 years ago: mechanical technology, linear processes with standard operating procedures and a far slower pace of work.
The way we work now is different. Companies are far more complex: from new technology and software to funky business models. At the same time, resources are being constrained and output and profit expectations are increasing.
Combine these things and we could worry risk might run away from us.
Technological tipping point
Thankfully, we are starting to reach a tipping point with technologies including augmented reality (AR), virtual reality (VR), just-in-time training and QR codes:
- AR enhances the capabilities of an individual digitally. With voice technology and body-mounted cameras, staff can speak to someone to check procedures, get help and assess problems.
- VR can simulate environments and give people realistic experiences in a very safe way. You can put people in ‘dangerous’ situations and teach them to address hazards safely.
- With just-in-time training, people receive information when they need it. Training 90 seconds before a task is far more effective than training six months earlier.
- QR codes can be scanned by new employees or contractors arriving at a site to open up and complete induction courses. They can also be used in work packs, with staff scanning a code for each step of a process to access short how-to videos.
These technologies have been around for a while now and increasingly piloted. The next step is mainstreaming.
New models for H & S
If I was designing H & S within an organisation now I wouldn’t have people based on every site. There would be a couple of key liaison roles, plus a central command post with the best experts on chemicals, working at height, crane operations, confined space entry and excavation available 24/7 to talk via AR headsets to supervisors around the world in real time. This model would be far cheaper and more effective than having people on sites managing paperwork.
We have worked with one company to rewrite their entire H & S manual into a Q & A format. AI technology allows us to track which questions people are asking most and explore what that means for risk across the business and what support and action is needed.
Five years from now, the way we do health and safety could be unrecognisable, without a single piece of paperwork. Everyone in an operational role could be wearing an AR headset, through which they access everything from how-to videos to hazard warnings, incident reporting to calling in expert support. Even without the AR technology, we can achieve all of this today with smart phones.
Improve work to improve safety
It is very hard to manage H & S with just our H & S processes and procedures. What contributes more to safety outcomes is the way that we plan and execute of work: the contractors we choose, quality of equipment, how we plan, the workflows we follow, the capabilities of staff in their core operational work.
There are many things that make work safe or less safe. We would label many of them as work processes and inputs, not safety.
Safety is an output of the work. To improve safety, we must improve the work.
The only way to get a true picture of safety and risk in a business is to understand how work actually happens – not what safety policies say should be happening or what managers think is happening. We call this ‘work as done’.
Organisations must have the capacity to:
- Guide and set the direction and expectations for work.
- Enable those expectations to be achieved by providing the resources, training, capabilities and capacity to execute the work effectively day in, day out.
- Execute all work effectively by making good decisions, communicating well and having competent frontline people to monitor performance.
Safe organisations must be psychologically safe too. If there is a free flow of information around a business, if everyone feels that they can speak up about safety to decision-makers, you are more than halfway to being a safe organisation. It is not easy to build this, but it is very important.
Less assessment, more control monitoring
The most important aspect of risk management is having the right risk controls in place. It sounds obvious, but it is often the most poorly done part of the process.
I have known organisations to spend 80% of the effort just identifying and assessing risks to get the paperwork done.
But assessing the risk is just the starting line. You haven’t really done anything to reduce the risk through that exercise. You have to challenge yourself to do more, to do everything practicable. 80% of the H & S effort should be spent making sure the controls are in place, known, effective and continuously monitored.
We always need to start with the work tasks and environment, to identify the hazards. Then you assess the risks, what the consequences would be and how likely they are to happen. Then you see what can be done to make those risks as low as possible. Finally, you put the controls in place, make sure they are working and monitored.
Often when incidents occur, it is because organisations have not spent enough time on this second part of the process.
Safety practices are important and we should do them as they were intended to be done, not as tick and flick exercises. They should always be well designed, well understood and well performed.
There are no comments yet