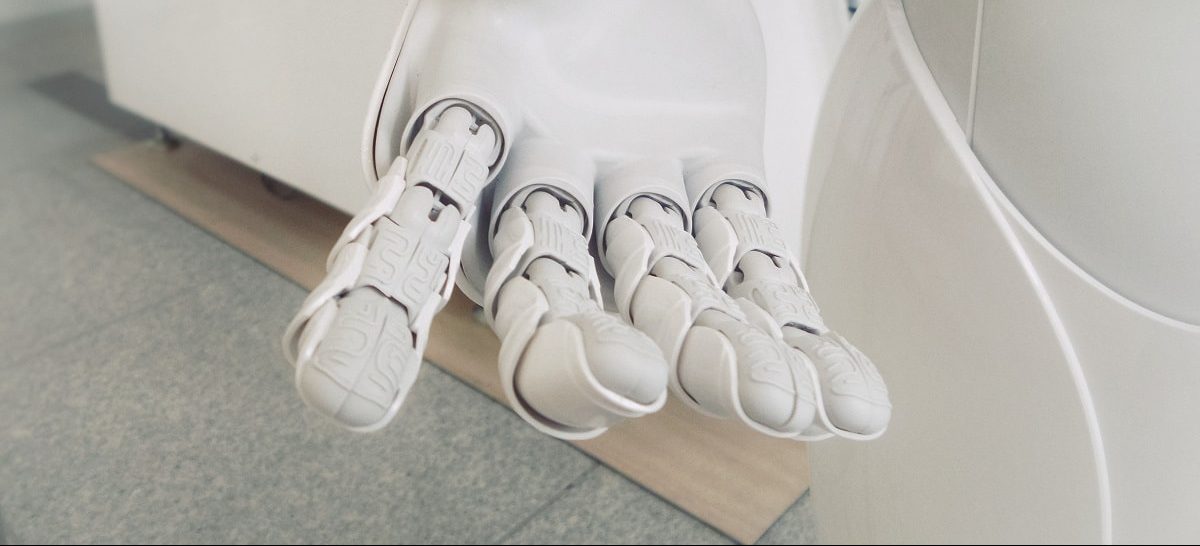
Today, we can say that robotics has become a part of day-to-day operations in managing large factories and facilities: from the hardest, dullest tasks to the most dangerous ones, robots make everything easier. According to Deloitte, 94% of companies claim that digital transformation is essential, as it improves productivity rates as well as operational objectives. In the field of large facilities, we’ve gone from analog to digital management.
Digitization includes a wide range of technologies for improving processes, everything from the Internet of Things (IoT) and big data to process automation, 3D printing, and virtual reality. There are so many examples: from using collaborative robots that make a factory’s production process much more productive, to using artificial intelligence to streamline processes and correct errors, as well as technology that reduces the amount of waste, thus helping the environment. This is why many companies have chosen to digitize most of their processes and incorporate technological advances. To delve into how technology is impacting the industrial field, its professionals, and managing large facilities, we’ll look at a few examples of leading companies that are operating in sectors ranging from aeronautics, logistics, and the automotive industry. We’ll focus on companies such as Ford, Siemens, Seat, and BMW.
TECHNOLOGY 4.0 FOR OPTIMIZING INDUSTRIAL PROCESSES
In the German city of Amberg, SIEMENS has one of the most automated, technological factories on the planet, where they combine artificial intelligence and data analysis to improve their processes. The plant specializes in producing Programmable Logic Controllers (PLCs) for industrial use, and it has managed to go from handling 5,000 data processes per day in 1995 to currently handling over 50 million processes.
MAVIVA, a leader in Spain’s logistics sector, has made advances in 4.0 management for its manufacturing processes, such as the robot designed to assemble windshields, which enables excellent levels of productivity. The company also has a 3D lab for monitoring in order to attain the highest quality possible for parts.
BMW has started integrating customer information into its production process. The automaker has offered its customers and other potential buyers an online platform where they can customize orders up to eight business days before the start of assembly without delaying delivery times.
FORD has turned its manufacturing plant in Valencia into one of the first in Europe’s automotive sector to completely eliminate waste that goes to the landfill. By using cutting-edge technology, the company manufactures about 400,000 vehicles annually at these facilities and has managed to prevent the Valencian plant from sending 15,000 tons of waste to the landfill each year.
The SEAT factory in Martorell, Barcelona, has 125 robots that are automated and carry almost 24,000 parts throughout the production plant every year. They can carry up to 1,500 kilograms, and they complete tasks right alongside factory workers.
AIRBUS uses augmented reality for assembling different models at its plant in Germany. The company claims that by using this technology, they have managed to assemble seats in their A330 model six times faster with fewer errors.
By implementing the CLOi SuitBot, LG Electronics has developed what are called exoskeleton robots that a worker can wear as easily as any other garment. With this technology, an employee can perform difficult tasks by reducing the weight on their legs and back, thereby improving their mobility.
Through its Innovation Lab in Europe, NISSAN has posed a challenge to different startups based on finding smart technology systems to help workers in their factories do their work more efficiently and productively. The purpose of the challenge is to come up with ideas for improving the relationship between people and technology in the new digital realm that the automotive industry is facing.
RYSIA has been working on 3D printing for the shipbuilding industry for a year. The company has three industrial 3D printers that are primarily used to produce prototypes of parts. The machines operate on an assembly line 24 hours a day taking models and producing one piece a day, a process that would take about a month without these machines.
These are just a few examples of what different sectors’ leading companies do. More and more companies are getting on the bandwagon with Industry 4.0, and moreover, there are more and more technologies being used to make companies more productive, more competitive, and more innovative – bringing the industrial sector into the 21st century. Sectors like the automotive industry, logistics, aeronautics and shipbuilding have already started to implement significant advances that go a step farther than their competitors, regardless of the sector they’re in or the sort of improvements involved in investing in innovation to advance their various businesses. In short, digital transformation is here to stay.
There are no comments yet