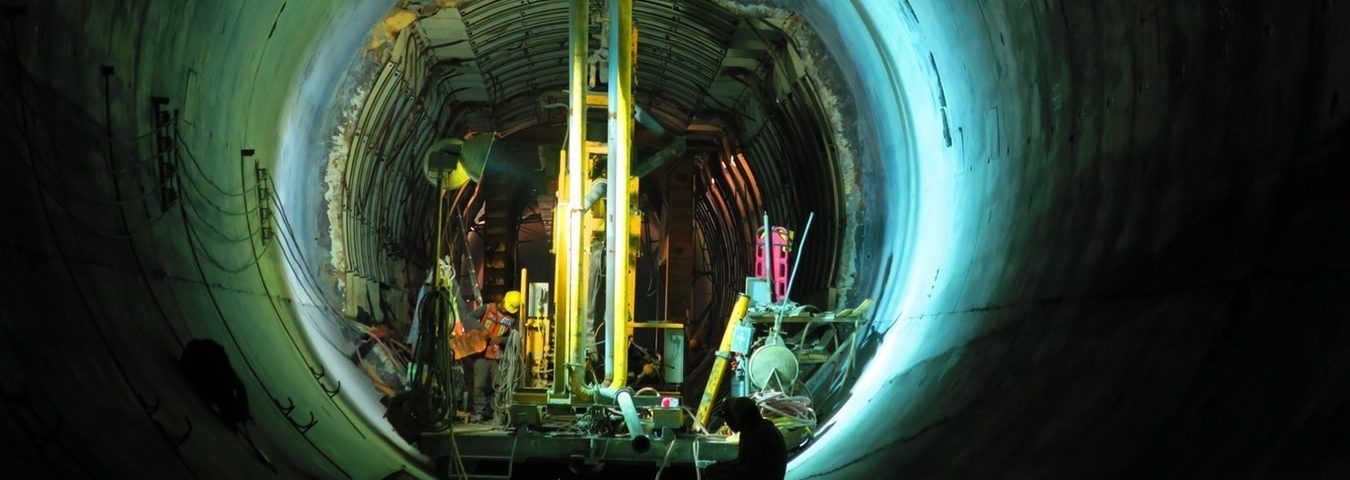
This European project, coordinated by the Robotics Laboratory of the University Carlos III of Madrid, brings together seven partners from five different countries for the purposes of designing and developing an autonomous robotics system that is capable of excavating, manoeuvring and mapping the subsurface. Possible uses for the robot include the construction of conduits, investigation of the subsurface and even providing assistance for search and recovery teams.
The BADGER Project forms part of the Horizon 2020 programme and constitutes an attempt to resolve a situation that is common to many cities, i.e. the need to drill underground with a minimum of exterior impact. The robot in question would be able to bore small-diameter tunnel networks – for fibre optics, electricity, water, etc. – without the costs and complications associated with digging trenches or having to dig up and re-lay existing installations. According to researchers this method of working is currently only used in 5% of urban construction projects, and its implementation on a more general basis would offer significant social savings in terms of both costs and a reduction in inconveniences.
Carlos Balaguer, a Systems Engineering and Automation professor and coordinator of the project, presents the idea, informally, as “a robot that looks a little bit like a snake and is capable of perforating the subsurface by itself using sensors and maps”. According to sketches and prototypes it does in fact look like a “large mechanical snake”, almost 80 cm long and 20 cm in diameter and comprising a number of interconnected modules: a drill head, a propulsion mechanism, a guidance system and a system for constructing supporting walls. Its name is BADGER, or RoBot for Autonomous unDerGround trenchless opERations, mapping and navigation.
An ingenious combination of technologies
The most interesting thing about this type of project is usually the types of technology that are incorporated, some of which may be cutting edge and some of which may already exist, and the ingenious ways these are combined. In the case of BADGER:
- The idea is to work underground and with independent movement, an environment to which the robotics sector is not very accustomed, having been used more in projects relating to surface, air, or aquatic environments. So this really does constitute unexplored territory for robotics.
- For autonomous navigation the robot uses georadar technology and digital maps to tell it where to drill. It is also equipped with sensors in an effort to avoid unforeseen problems such as rocks or existing underground installations. The robot also uses Ground-Penetrating Radar (GPR) and a number of Inertial Measurement Units (IMU) to calculate its location with respect to its surroundings and its physical position in 3D.
- Proper tunnel construction requires reinforcement of the walls where the drilling is carried out, and the idea in this case is to use 3D printers in one of the modules to «print supporting walls» as the robot advances. These 3D printers use materials such as concrete and have been successfully used in many projects to date.
- Drilling techniques are varied and interchangeable. The robot’s modular design means the drill heads can be changed, depending on the type of terrain, so the device can use rotary or impact drilling. There is even a tool specially developed for the project that uses ultrasound to pulverise rocks and other debris.
BADGER was conceived with the idea of minimising exterior impact, the one maxim being «not to dig trenches». This is known as trenchless technology, the basic idea being to avoid noise, dust and traffic interruptions and diversions, all of which can be problematic, and even dangerous, for the general public.
How BADGER works
As can be seem from the preliminary designs, the underground robot consists of a number of modules united by mechanical couplings that give it flexibility and mobility; a mechatronic system that allows the drill head to move and turn in all directions and at all angles with maximum manoeuvrability, meaning the robot can turn and manoeuver in open and closed angles, as required. Another important aspect is that it can operate with severe gradients. The typical depth that the device can reach is some 5 metres below the surface.
Although the robot is autonomous, it is operated via a control station at all times, a computer that carries out all the supervising and planning tasks in addition to creating a digital representation of the surroundings and any recognisable objects it encounters along the way. This is achieved through the use of available digital maps of both the terrain and the electricity, water, gas and sewage systems in the area in question. The robot also uses a conventional radar system to map the subsurface before drilling begins.
The device is connected to the exterior via a long cable that is used to provide the system with both electrical power and data transfer (the central station also features wireless connection). Excavated and pulverised material is extracted via a conduit equipped with a conventional pumping system. Both the cable and the extraction conduit are long enough to follow the robot wherever it needs to go.
Beyond little tunnels
The BADGER Project may eventually constitute an acceptable solution, thanks to reduced external impact and the fact that it is a reasonably inexpensive way of excavating small tunnels and conduits. But it is more than that. Among other aspects, the project has, for some months now, served as a meeting point where engineers and scientists from diverse disciplines can come together on a joint project. These include experts in robotics, information technologies, georadar, drilling and civil engineering, and even artificial intelligence.
Time goes on, and while the ambitious objectives of the project are gradually being met – these began with the initial design and prototypes – many challenges still have to be met before the project can culminate in an autonomous, modular, reconfigurable, versatile and flexible robot.
As an added bonus, and one that falls outside the realm of civil engineering, those responsible for the project have indicated that the robot may also turn out to be useful in terms of collaborating in search and rescue operations. For example in the event of landslides or when there is a need to access, explore or map places that are inaccessible for personnel, but maybe not for a little, intelligent, subterranean robot.
There are no comments yet