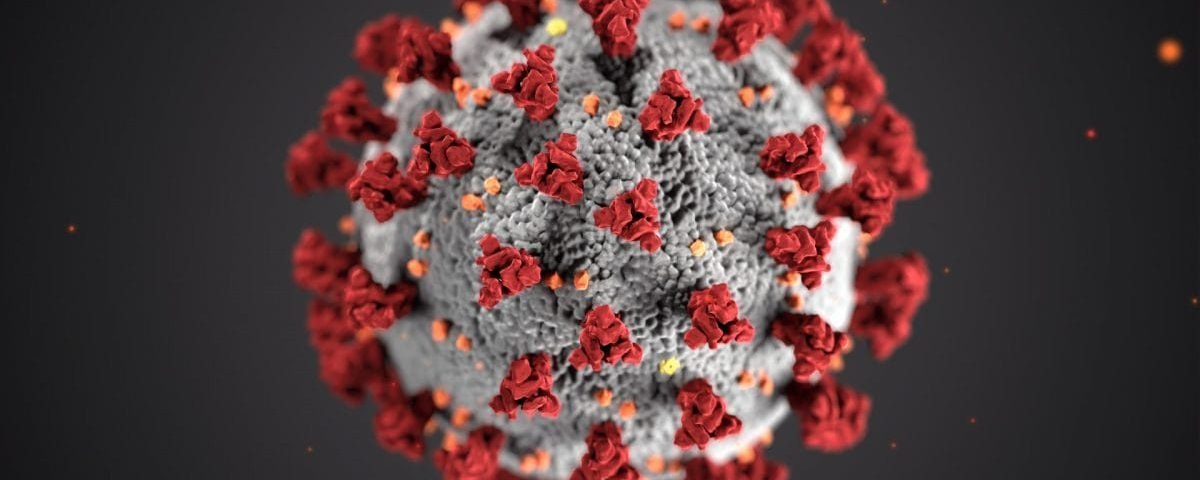
March 16, 2020. The schools are already closed. Full-blown confinement is coming. Newspaper headlines announce that it is a significant risk to leave the house since we may come into contact with contaminated surfaces anywhere: the street, public spaces, and so on.
A few days earlier, Ferrovial had told us to do everything we could think of to fight the virus. At that time, they were talking about infrastructures, helping out with the field hospital at the IFEMA fairgrounds, manufacturing 3D masks, visors, respirators, etc. Then, I thought that those of us at Ditecpesa, a company specializing in chemistry, couldn’t do much to help. Honestly, we felt a bit frustrated.
While reading the news that March 16, I had an idea. Would it be possible to apply something that sticks to infrastructure and kills the virus? The basic idea was doing everything we possibly could. We had been working on solutions for chemical adhesion for four years, after all. The big difference between that and conventional disinfection is that it is instantaneous. When it is first applied, it works well. A short time later, though, it is no longer on the material, and if someone who is infected touches it, the viral load is deposited there. It should be noted that the Murcian Institute of Biosanitary Research (IMIB) recently found COVID-19 on hospital surfaces, despite routine periodic disinfection.
Every solution starts with an idea
We started talking with a start-up we had worked with before over the years. One thing was clear to me. The core concept was “developing an effective, industrializable product at a viable cost that can be applied widely in public spaces.” It would be useless to make an R&D molecule that couldn’t be industrialized later. The truth is that this is a pattern we follow in everything we do at Ditecpesa. After hundreds of hours of perusing scientific publications, we saw a window of opportunity via several commercial products that we could try to produce in a water-based formula. A water-based formula would be ideal for making general application possible – we can’t distribute something dissolved in organic solvents.
I proposed this idea to Ferrovial’s team. The answer was: “full-speed ahead with this idea.” A few days later, we spoke with the CDTI (the Spanish Ministry of Science and Innovation’s Centre for the Development of Industrial Technology). By March 26, we’d crafted a research proposal, and on March 30, we had a meeting with the company’s senior management. On April 6, we set to work in the Madrid Science Park’s chemistry laboratories.
In May, we had the first formulas. We realized that we needed a specialist in microbiology to move forward quickly with the project. This was because outsourcing biological tests involved very long waiting times. We were lucky enough to find another microbiology start-up that could help us. From that moment on, things moved at a fantastic pace: every week, we made formulas and tested them on different materials: glass, plastics from the Zity Renault Zoe (we chopped up all sorts of parts, including a whole dashboard), steel, stainless steel, and ceramic. We had results every Tuesday and Friday. To date, we’ve done over 1,000 experiments on different surfaces.
Initial tests and results
In this phase, we had already realized that it wasn’t only the chemical formula that was key, but the application technique. This ensured optimal adhesion in the right amount. We tested out all kinds of surface application systems.
By May, we had a product that all the scientific studies and tests led us to believe would work. We presented the project to an urgent meeting of the European Commission’s European Institute of Innovation and Technology (EIT Urban Mobility). We were among those chosen to develop real-world applications in 6 months (July to December) at maximum intensity and speed, as the situation required. We registered the formula in August so that it could be used in public spaces. On September 30, we begin the first real applications in Barcelona’s Metropolitan Transport.
That formula already has a trade name: Long Clean Surface. We look forward to applying it in as many places and countries as possible.
To date, it has also been applied to Madrid’s fleet of 800 Zity vehicles and Ferrovial Construction’s offices.
How does this sanitizing solution scale?
Let’s rewind for a second. The initial industrial manufacturing started on July 8, 2020, to make sure that what we’re doing on a small scale in laboratories will work the same when manufacturing 1,000 liters. We were checking to make sure everything would work like in the lab. At that time, we had tested permanent disinfection on all types of microorganisms: bacteria, fungi, viruses, etc. We had to do the definitive test with the coronavirus. We asked to do this in mid-July. Given how difficult it is to get a vial of the virus, it arrived on September 18.
Since then, we have been working in a secure laboratory, fine-tuning the highly complex test to obtain conclusive data. Finally, on November 14, 2020, the test was completed, and we began to have the first positive results. We could finally conclude that the compound we adhered to the surfaces is effective and kills the coronavirus. It has taken 243 days of work, many hours in the lab, and constantly thinking about it seven days a week.
We are quite pleased. Numerous problems have been handled over these 243 days. What makes us truly content is knowing that we are already truly helping to fight the pandemic where this solution is being applied.
We’re dedicating this entire project and effort to our colleague Teo, who is no longer with us because of the virus. The last conversation I had with him was about getting the screens that Ferrovial Construction had manufactured at its machining service to healthcare workers. This just goes to show what an excellent person and professional he was.
How much does surface contamination impact the transmission of COVID-19?
I have been working on this for months. Like many other things, it isn’t very clear. It was even thought to be the primary factor at the very beginning, and now it seems that aerosols are more important. We must continue working on this to understand the virus’s mechanisms – how much infection occurs by direct contact, how much is by droplets and aerosols, and how much is due to contact with contaminated surfaces.
On April 16, 2020, The New England Journal of Medicine reported that COVID-19 could survive on plastic for up to 72 hours and on stainless steel for 48 hours. There have been many subsequent studies on this. The most striking is one by Australian researchers, published in the Virology Journal on September 22, 2020. They found that, under favorable conditions, the virus can survive for up to 28 days. Recently, TUFTS University published a study on medRxiv that was done in a city where coronavirus was found on 25% of trash cans, 12.5% of subway doors, 13.3% of banks, 10.4% of traffic light buttons… Reading this surprised me. If the coronavirus could shine, we would see it covering so many surfaces like glitter.
In the end, I’ve come to the conclusion that it doesn’t matter much if it’s 50%, 20%, or 0.2%. We know that viruses are spread on surfaces, and whatever the numbers are, we will strive to reach our goal of totally eliminating it. Any percentage at all is important to us.
Moving forward
We’re going to continue in this line of research. We can do our part, adding permanent chemical disinfection of surfaces to other preventative measures and vaccines. Hopefully, the pandemic will end soon. We will continue working to stay prepared and to protect people and infrastructure mobility.
As Bill Gates said in his 2015 talk, we must remember that today’s world is global, increasingly populated, and highly mobile. This means that microorganisms like the virus have some quite favorable conditions for expansion, and we must develop technology to combat them. A virus is a dangerous enemy – an invisible one. This really hits home when you start doing tests. Another major thing I’ve realized is that knowledge is the key to facing problems. This is more and more true of scientific knowledge in particular since the threats are becoming more and more complex.
We would like to thank everyone for their assistance: Ferrovial, family, friends, companies we’re working with on this project, public resources, and the dozens of people who have participated in this ongoing project.
There are no comments yet