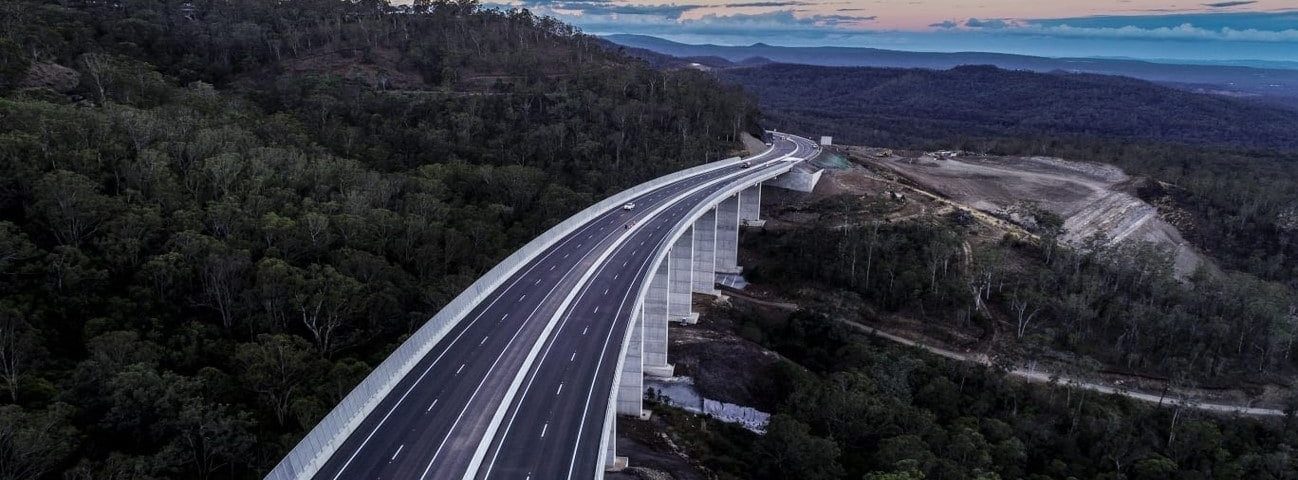
When you design any infrastructure, you must consider the different ways you are going to build it. This is your construction methodology.
On the Toowoomba Second Range Crossing road project in Queensland, Australia, one of my roles was to build the viaduct. But my team was involved in the design phase too, to ensure the build would be easier and safe, more cost effective and completed on time and on budget.
Preliminary works
Once the design was about 60% done, we were able to start construction. Preparation work included ground clearing and grubbing, arranging construction access, sourcing suppliers for concrete and girders. That was back in March 2016.
We also did an extended geotechnical study to assess what was in the ground. This affects the depth you need to drive the in-situ piles, their length and where they can be placed. In the Toowoomba Second Range, there were many important things to consider – the type of rock, the potential for landslides and even an underground gas line.
We designed our piles to avoid any issues in the area, but also used appropriate methods to impact any type of geotechnical issues in the area, such as two adjacent active landslides. We positioned piers 17 and 18 of the bridge to sit on both sides of the gas line and far away enough to avoid any complications.
The viaduct spans 800m of very difficult terrain, with a particularly irregular and steep incline – a 35% gradient running longitudinally and in cross section.
With this kind of slope, the construction methodology played a very important role to help identify the location of the tower cranes, the type of methods to lift the reinforcement, formwork, girders, access and egress to the piers and headstocks, including the study and installation of sediment control measures to guard against washouts or exposure of the foundations during rainstorms.
From the top
One of the most important things we did in this project was to provide good access to build the viaduct’s structural elements and allow for concrete and girder delivery, as well as other materials that were needed. The accessibility of the construction works was very difficult, which made the delivery and installation of the 32-38m beams with cranes a very challenging task.
We decided to work from the top of the bridge and not from the bottom, placing the Super T beams using a launching girder from the south abutment. This is an established technique in bridge-building when operating in difficult terrain but launching 90 tonne beams down such a steep incline bridge (6.5%) was an additional task that made the whole operation even more complex.
Due to gravity and the pendulum effect, girders can swing out of control if you don’t design proper hooking points and tie-downs to avoid this movement. A big innovation on this project was to be able to do this safely.
Since the bridge deck required a continuous pouring to keep launching girders in the next spans, we built the bridge one span at a time. This forced us to work on a fixed and rigid construction schedule, which any delay will impact the completion end date.
The viaduct and the beams we used were designed for this specific launching girder machine, as we knew the spans could be no more than 38m long and the girders no more than 90 tones.
48 hours
Another considerable challenge was the Queensland Rail track, which crosses under span 22 of the viaduct. We had to give a 4-6 months’ notice for a 48-hour shutdown of train services. We needed to ensure this section was complete within that window to avoid a major delay of the viaduct’s completion date.
We knew if things didn’t go to plan on those two days, it would have delayed the project for months. Finishing that section within the time was a huge milestone.
For the viaduct to be built we needed to come up with practical solutions to a range of challenges: geotechnical, economical and with accessibility.
Thinking outside the box
As an engineer, I always build with practicality in mind.
This project allowed our team to think outside the box and improve our knowledge. Our superiors encouraged us to come up with new techniques and incorporate them in the project. This not only helped us grow as engineers and construction professionals but marked a major innovation milestone for bridge design and construction, as a machine extrude the bridge concrete barriers, the first time in Queensland, allowing us to complete the bridge on time.
Our clients – the Queensland Government and the Government of Australia – had originally envisaged a tunnel for this stretch of the road. However, our proposal included a cheaper and more practical alternative, which was a major feature that helped us win the project.
It’s all about teamwork
Being able to complete this project successfully and on time was in large part down to our team, which was like a family to me. The fact that we didn’t bring in any special company to build the viaduct is a clear example of our ability to execute a complex project in-house and with people we could really trust.
Even though the team and I had never built a viaduct before, we not only proved to ourselves and to the world that we could do it, but that we could build something truly iconic.
On the day we finished the bridge, my senior manager and I drove across it very slowly, so we could look at all the work we had done and reflect on the challenges we had overcome. It is hard to describe in words the satisfaction you feel on completing a $1.6 billion project. Let’s just say it felt pretty good.
The Toowoomba Second Range Crossing was designed and built by Nexus Delivery, the Construction Joint Venture of Nexus Infrastructure which consists of Acciona Infrastructure Australia and Ferrovial. It is funded by a public-private partnership with the Australian and Queensland Governments. It was opened to the public in September 2019.
There are no comments yet