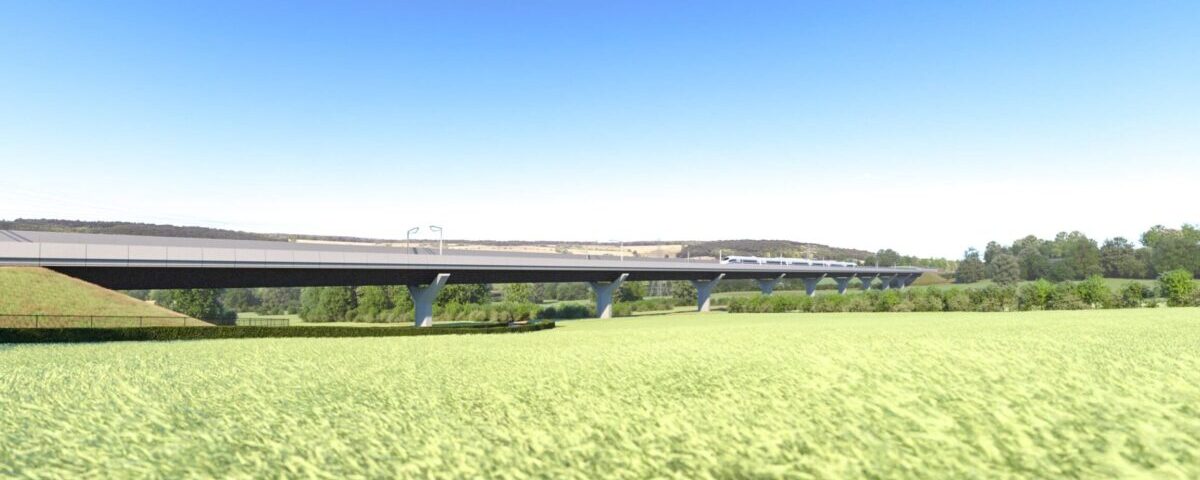
Good design encompasses efficiency, sustainability, and safety, among other things, in addition to offering a visual appearance that’s in accordance with a project’s requirements. The plan to build the Thame Valley Viaduct, part of the United Kingdom’s HS2 railway line route, has managed to combine these four attributes while firmly committing to innovation.
Along with our partners, our company has played a fundamental role in redesigning this viaduct. It will rely heavily on prefabricated construction to achieve the major objectives of the HS2 project: connecting the United Kingdom’s major cities by high-speed trains and leaving a legacy for society and future generations.
Redesign for better efficiency
The United Kingdom has a major project to bring high-speed trains into the region. It’s doing this with high requirements for technical and quality factors, as is the case for a country with extensive railway tradition and experience. It’s called HS2, High-Speed 2.
The first phase will link the cities of London and Birmingham. As part of EKFB – a team made up of Eiffage, Kier, Ferrovial Construction, and Bam Nutall – and working closely with its design partner ASC – Arcadis, Setec, and Cowi – Ferrovial is in charge of carrying the project out and building two central sections of its first phase.
These will include a part that is particularly relevant due to its approach and dimensions: the Thame Valley viaduct. Thanks to the global nature of our company, its international knowledge management, and close collaboration among the client, the contractor, and the designer, the original design was modified to propose another more innovative, more efficient solution based on prefabrication of many of the elements.
On the one hand, this commitment to prefabricated construction aims to increase quality and safety by building the parts in a more controlled environment and to reduce the amount of work done on-site. On the other hand, it’s to enhance sustainability and efficiency by employing fewer means and resources and to lower the impact on the land and the environment.
In addition, the project’s redesign has highlighted the visual impact, striking a balance between functionality and appearance. This is an important point since the viaduct crosses a rural area of special interest that the River Thame (a tributary of the Thames) also passes through. It’s located near residential areas and the town of Aylesbury.
880 meters of prefabricated construction
The plan to erect this 880-metre-long viaduct – the largest of the entire section – includes establishing the concrete foundations on-site (pilings and capped piles) in a way that’s very similar to the one proposed in the original project. However, the elements of the substructure are already prefabricated components; these will not be created in the work environment.
This way, the 35 concrete pillars that will support the viaduct will be placed directly on the foundations, forming a perfectly joined structure. This is a much faster, cleaner construction method that has less impact on the ground. It also saves time, reduces costs, and improves safety by limiting the number of tasks done at height.
Another significant piece of this project is that it has a deck with high levels of prefabrication: the mold itself (a lattice formation floor plate) is made of concrete, and it’s part of the final piece. This reduces the number of operations and makes the work safer and more efficient. This procedure is already used in Spain and the United Kingdom, but in this case, the innovation lies in the fact that it has been extended to the entire width of the deck, including the side overhangs.
Finally, another major change from the original to the final plan is that the number of box girders was brought down from four to two. The diaphragm on piles has also been eliminated by providing continuity between adjacent spans through the use of post-tensioned bars. This gives rise to efficiency in construction and aesthetics by visually concealing the supports from the outside of the viaduct.
In short, this measure limits the number of elements and results in a much cleaner, more elegant construction. In other words, it significantly improves the viaduct’s aesthetics. In addition, this solution reduces the carbon footprint (by increasing efficiency in prefabrication and reducing the volume of materials), as well as environmental conditions in the surrounding area during construction.
Experience, partnership, and new approaches
HS2 is, in its entirety, a project of great technical complexity that requires experience and partnership. In the case of the Thame Valley viaduct, our company has gathered its knowledge and experience from other locations to come up with a safer, more innovative, more sustainable, and more efficient format.
It’s done so through partnership and joint work in every part of the project. The role of Tomás García, Head of Civil Structures for HS2 Ltd and of the design team for the EKFB TJV, led by Jose Vicente Candel and Ignacio Chicharro, was especially significant. They were familiar with this way of building and were essential in achieving the implementation of all the changes that have made the final design possible.
In short, cooperation among the client, contractor, and designer has been key to finding this aesthetically and technically improved solution for the Thame Valley viaduct. Once built, this project will serve as a support for the trains that will link London and Birmingham at speeds of up to 360 kilometers per hour.
There are no comments yet