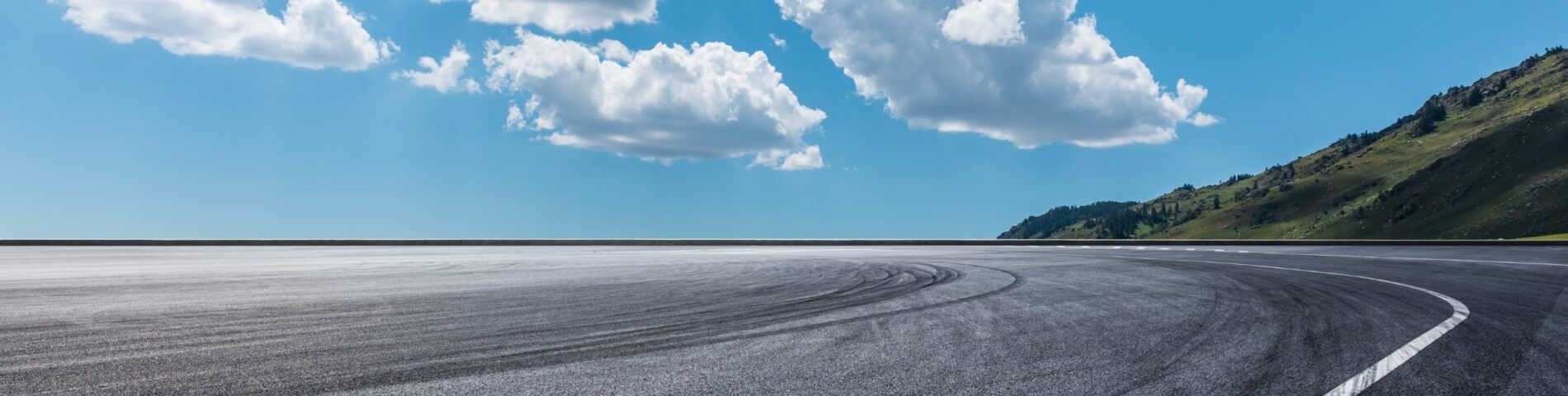
In 2016, we were lucky enough to have the opportunity to start writing posts on the Ferrovial blog, and we already have a total of 16 posts. Looking at these as an analogy, they could be a discography where there always seems to be a common denominator in many of the songs: a focus on the environment.
Currently, large companies, governments, and sectoral associations are focusing on achieving zero emissions, including oil companies, with sights set on 2050.
The road sector is, too. The NAPA (National Asphalt Pavement Association) created its own manifesto for this American association of manufacturers looking towards zero emissions.
NAPA’s document would contain the most important songs of the 16 posts we have written over these years, so I thought it would be good to make a compilation of the most important ones. This entire set of measures we’ve explained are measures that we have to make our own as a society – governments, companies, and citizens – to have even more environmentally friendly roads.
Let’s start with the big successes in these 16 posts: the measures that we as a sector must carry out.
The ten keys to achieving zero emissions:
-
Pavements that last a long time
The first thing is something that, for me, is at the heart of the idea of environmental pavements. The floors must be long-lasting, and recycling has to happen as late as possible. We explained this in Pavements and the environment or recycling – yes and no, long-lasting pavements first!
Then, there’s another action that’s well-developed and integrated into roads: bitumens modified with polymers that are of higher performance and higher duration than typical ones, which we explained at the Argus conference last year. They allow for thinner and longer-lasting pavements, and their use would have to be more widespread; right now, it may be around just 10% of roads. Roads can cope with extreme weather – Ferrovial Blog
That is the most important thing for me, and it can be applied to anything in our society. Things have to last. It would be absurd if recycling led to them being consumed even faster.
In fact, in his post on the blog Are we sustainable at Cintra? What I think as CEO (ferrovial.com ), the CEO of Cintra has an identical vision: “infrastructure, by definition, is something that’s designed to last.”
-
Recycling
Secondly, we have to recycle as much as possible. On the blog The highways of the circular economy, we found this: “asphalt pavement can be recycled infinitely many times.” In today’s society, we try to recycle for the same use or a different one while trying to attain the highest possible %, though it isn’t usually very high. In the case of asphalt paving, while it can be recycled 100% for the same use, this is an ideal situation.
The 2016 post The way to implementing green pavements on highways for society’s environmental and economic benefit says, “whenever I’m driving along a road and see the opening of the aggregate quarries in the mountains, I wonder to what degree this would have been preventing if the recycling rate of roadway was higher.”
How do we maximize the % of road recycling?
The techniques are quite varied, and depending on the type of continuous asphalt surface, with its multiple variants or discontinuous versions, the answers may be different. On the one hand, we need to have an asphalt surface adapted to it. It is usually manufactured with a % of recycled agglomerate, depending on the standard and situation, but saying “the more, the better” holds true, with different systems having reached up to 80% of reused product ideally. For example, at the Ferrovial Construction Machinery Inventory plant pictured in this image, the entire system proposed is what is called “Cold Recycling,” a mixture where the milled agglomerate is first introduced to the mixer, where it is then mixed with the aggregate and virgin bitumen to obtain the final product with a significant rate of recycling.
Here, we’ll make an aside to remind you how asphalt agglomerate is manufactured, as explained on the blog Roads can handle extreme climates.
And then there’s the chemistry of bitumens. When we recycle, we get aggregates and bitumen; the latter is a little aged and hardened. The bitumen to which we add the new agglomerate must have a set of rejuvenating oils that serve to interact with the recycled bitumen, soften it, and help it mix well with the new bitumen.
The latter are known as bitumens with rejuvenators for mixtures with recycled agglomerate, and they’re essential for meeting all the properties required of the roadway.
-
Lowering manufacturing temperatures
We need to lower manufacturing temperatures, and while we can accomplish this with different methods, we’re convinced of two. First, there’s providing the asphalt surface with a foaming system so that it produces bitumen foam before entering the mixer. This is achieved by injecting a small amount of water under pressure; this bitumen foam helps mix the aggregates by reducing viscosity and therefore requires a lower temperature for mixing with the aggregates. On the other hand, bitumens with low viscosity or surface tension are used with aggregate. Both cases also make it possible to reduce the manufacturing temperature of the asphalt surface.
-
Natural products for bitumen
To date, bitumen is the best and only conglomerate for making pavements; though it has no substitute, it can be recycled forever. But to take things further, we have to look for natural products that can be incorporated into bitumen. There are studies on using plant waste and various kinds of by-products in the industry, but all this is possible only if the quality is the same or greater, never lower; otherwise, it wouldn’t be justified since the material would last for less time. Companies like Shell are putting a lot of work into lowering emissions from the entire asphalt pavement process.
-
Using renewable fuels
Beyond bitumen and aggregates, which are the raw materials for pavement, the use of alternative and renewable fuels in asphalt surfaces should be encouraged to reduce carbon emissions.
You may have read articles on how even the aviation sector is working in this field https://www.cepsa.es/en/utilities/catalogue/aviation-fuel.
-
Improving the transport efficiency of trucks and boats.
Moving forward in adopting advanced logistics technologies to improve the efficiency of trucks means that their use on routes between the agglomerate plant and the construction site must be optimized, with no stops and just in time.
Then, there’s another logistical factor: you have to get things from as nearby as possible; we will have to bring both aggregates and bitumen from the closest source. If the aggregates aren’t perfect, we will try to improve it with the agglomerate formula.
Bitumen transported globally by ship is a complex case: there is enough supply but fewer and fewer production points. This is because refineries optimize some products and others to be more efficient, so there are quite a few logistical tensions; shorter transports will be more environmentally friendly, even if they’re a little more expensive.
-
Best practices in construction
Identifying best practices to reduce the energy consumption of equipment during the construction phase; spreading and compacting equipment, incorporating automatic reading and pass control equipment, state-of-the-art engines, the transition to electric and/or hybrid equipment, etc.
Using fleet control systems for transport trucks to optimize routes and the number of them.
Monitoring the carbon footprint of the raw materials used and developing sustainability certifications that help employ manufacturers who strive to work on achieving environmental objectives.
-
Taking climate into account in the design
Being quick and decisive about design change decisions with climate change is key; currently, a firm can deteriorate if we do not consider the change in climatic conditions that are already indispensable, and we would have only a short road ahead, not the long haul we envision.
-
Improving mobility
We must improve mobility, and this requires optimizing cars. Minimal use of each car over its temporary lifespan doesn’t make sense; manufacturing fewer cars would significantly reduce the emissions of that production process.
-
Connected infrastructure
Infrastructure that is fully connected to the majority of vehicles will make it more efficient and help improve mobility. Here, Ferrovial is leading the way with its AIVIA Orchestrated Connected Corridors initiative.
Our growth here is evident. First, we went from the basics for materials, such as reusing them, to the organizational scale of large infrastructures as a whole that’s carried out at AIVIA, but the solution incorporates a linear combination of these ten factors. They are all important and have to be worked on at the same time in a package of joint measures to achieve the decarbonization of roads as a whole.
There are no comments yet