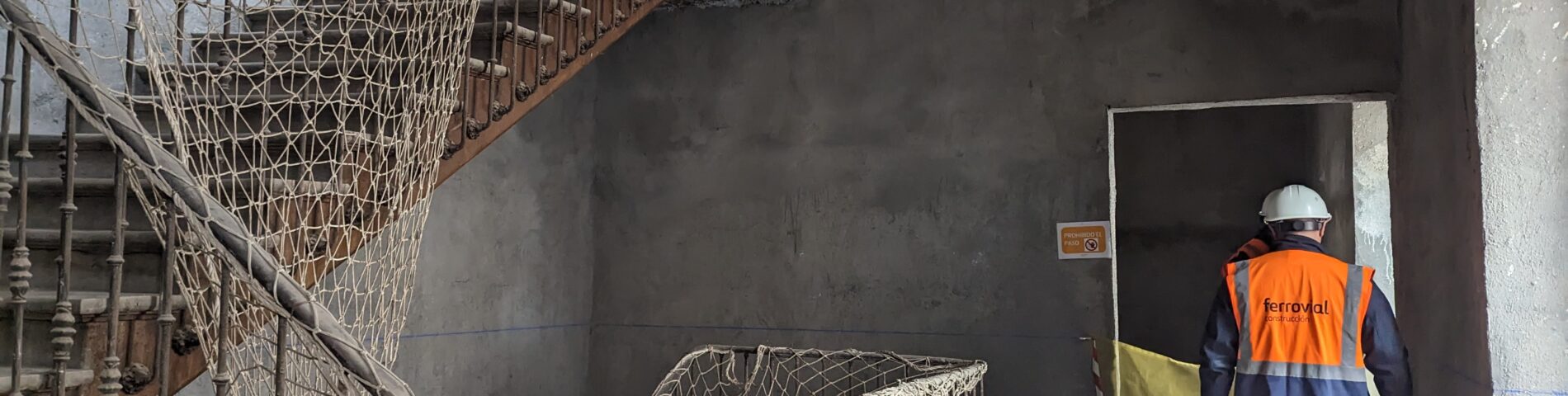
Challenges of renovating the Duchess of Sueca Palace II: logistics in the heart of Madrid
17 of April of 2023
The center of Madrid is a window into history: many of its buildings are home to past lives that we often don’t know about. One good example of this is the Duchess of Sueca palace. Since its construction at the end of the 18th century, it has been everything from a school for the children of those who worked in the Royal Home to one of the most famous settings from the ‘The Ministry of Time’ series.
From the street, you can’t see all the building holds behind its facade: like an iceberg, we can only glimpse a small part of the whole. But inside, it has several patios and structures made with unique methods that are very unlike the ones we usually see today.
In another post, we’ve explained how, after taking a look at the past, we renovated this building by imitating its original construction methods. In this one, we’ll tell you how we dealt with a long list of logistical challenges in the heart of Madrid to bring new life to the Duchess of Sueca Palace.
Courtyards, pedestrian streets, and a protected facade
Walking to the Palace of the Duchess of Sueca is easy. You simply have to go to the center of Madrid and walk down a street brimming with life, just a few hundred yards from Plaza Mayor. Getting there with big trucks loaded with construction materials and equipment, though, presents all sorts of challenges.
First of all, the vehicles must be small to navigate the one-way street, and the companies associated with the project have to manage their own permits to travel in Central Madrid. Once in the building, you’ll find a granite facade that was protected and recently restored – in short, it cannot be altered. The only way in is through a large wooden door.
Inside, the Duchess of Sueca Palace has several courtyards. We had to carry out a large part of the reconstruction and renovation work right here in one of these right in the heart of the building. The difficulty of getting to this part of the city and inside the palace with large vehicles forced us to pay special attention to organizational and logistical tasks that are no great difficulty in other projects.
Renovation on the Duchess of Sueca Palace was set up like clockwork, where no one gear could fail. It worked perfectly thanks to our search for alternative solutions and teamwork.
The first challenge: transporting the materials
Moving the materials and machinery needed to renovate the building was one of the biggest challenges in this project. The limitations started with a basic as necessary as concrete. To be able to work in the courtyard, the vats had to be small – just six cubic meters. Nowadays, there are very few concrete mixers of this kind since they aren’t profitable, but we finally managed to get hold of some. In some specific cases, we even pumped the concrete from the street into the site’s interior.
We also found it difficult to stock up on bricks. We had to hire them through a distributor since the direct manufacturer could only supply us with large quantities. We organized a daily delivery of about eight pallets so that the supply was practically continuous.
We also got iron in small quantities. We couldn’t bring the parts pre-made from the factory, so we had to assemble them once they arrived. We would bring them through the door, put them together ourselves, and then pour the necessary concrete. The wood, on the other hand, had to be shipped to a logistics center; from there, it was transported to the construction site in small trucks that could transport a maximum of 10 pallets.
All this made us approach the site like a puzzle. We had to make sure that the logistics worked perfectly and that the delivery schedules were tailored to the rhythms of construction.
The challenges of assembling the crane
Once the challenge of moving the materials was solved, an even greater one arose: how could we get a crane inside the building? The alternative, loading the materials like they did in ancient Egypt, was not possible. It would be so labor-intensive and complicated, plus the costs would skyrocket. We had to find another option.
After considering different possibilities and weighing different options, we decided to set up the crane in the large courtyard. We measured its size to make the most of the space we had and thus optimize operations. To assemble this main crane, we installed a City crane in the small courtyard. It rotated on its own axis, and this allowed us to work in small a small space.
To bring the pieces, we set up a distribution chain that went from a nearby square to the site’s interior. The first stop along this chain was the trailers that moved the materials to the area. These were loaded in a smaller truck that carried the materials to the small courtyard in the Duchess of Sueca Palace. Then, a final truck would take them into the big courtyard, where the City crane would assemble them.
Once organized, the process worked perfectly. We started at about 5 in the morning to interrupt life in the area as little as possible, and we finished getting the parts in by about noon. By the afternoon, the crane was already set up.
Thanks to solutions like these, the Duchess of Sueca Palace will have a new life: it is expected to house two social centers, one to accommodate families at risk of exclusion and one for the elderly.
Renovating it was undoubtedly a fun, different sort of project. When you face new problems, situations that are scary and demand respect, work becomes a challenge. It forces you to get active, investigate, ask questions, and study to find solutions you’d never imagined before. It also leads you to collaborate and work as a team to give everyone the best possible options.
There are no comments yet