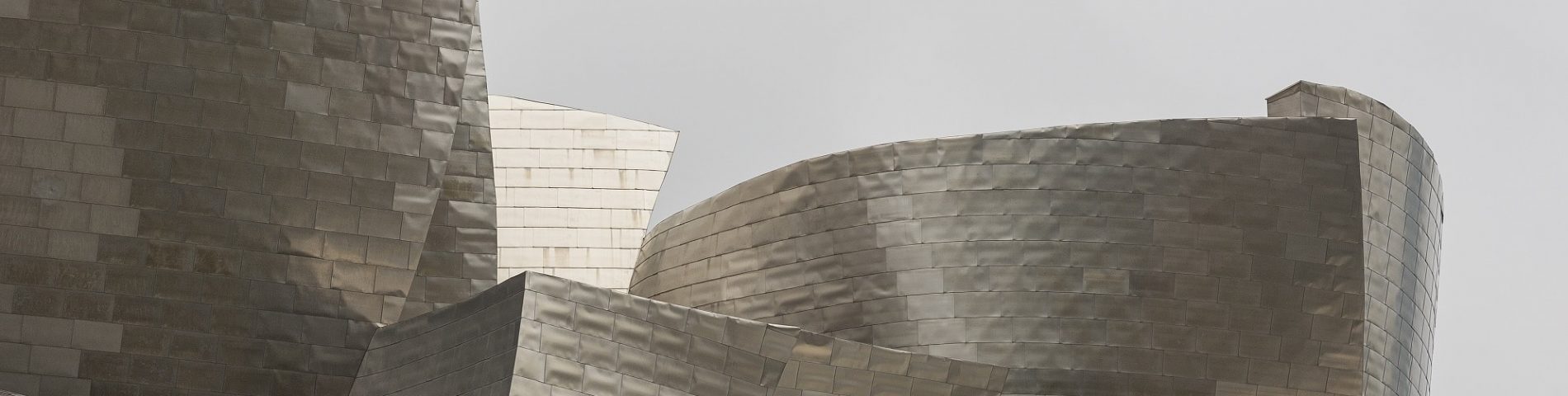
Bilbao’s Guggenheim Museum opened to the public for the first time on 18 October 1997, exactly 20 years ago, with an exhibition of 250 contemporary works of art. It is not the only Guggenheim museum: there is also one in New York (1937), in Venice (1980), and a new one being built in Abu Dhabi.
Travel back to Bilbao in the 1990s. Computers in offices still had those bulky screens, Internet connections spluttered with a characteristic wheeze every time we connected through the telephone line, and design programmes left a lot to be desired.
Yet, despite all this, a Guggenheim was built to provide a beacon of light which transformed Bilbao. A venue which today receives more than a million visitors on average per year and which served to “put Bilbao truly on the map”. This building amazed the world in 1997, and still amazes today. But do you know how a Guggenheim is built?
The Guggenheim Bilbao in numbers
Significant numbers are always worthy of note, and some of the numbers for the Guggenheim Museum will leave you at a loss for words. Starting from the bottom, from the skirting which comprises the building foundations, more than one thousand supports can be counted, with 665 pilings, 444 pile caps and 181 micropilings holding up the set of buildings making up the museum. Yes, the Guggenheim is just one museum, but it is comprised by an amazing combination of interlinked rooms and halls which merge and intersect in one same space.
It may seem like the number of supports is excessive, but if we take into account that 25,760 metric tonnes of concrete and 58,820 cubic metres of formwork were used, it makes a lot of sense. In addition to aggregates, there is a metal frame weighing in at 3,256,395 kg, and several other metallic structures weighing 4,854,800 kg.
That’s a lot of tonnes. And then there are reinforced concrete beams spanning more than 1.5 km, metallic cladding made up of more than 42,875 titanium panels to cover a surface area of 23,530 m2 , and outside stone cladding covering 14,505 m2.
To say nothing of the facilities, temperature control and mobility systems, the interior fittings, or the 416 km of cabling which run through the building (and which are no doubt pretty heavy too). Plus 46 360 m2 of interior floor paving, using stones and tiles. These numbers are difficult to take in, but we nevertheless have to add one more: 20, the number of years for which the museum has now been open.
Here’s how the Guggenheim in Bilbao was built
Put yourself in context: you’re Frank Gehry and you know what shape the future Guggenheim museum will be, both inside and out. You’ve designed it using simple materials such as wood and plaster, and it has a whole host of totally unconventional shapes, looking like the nearest thing to chaos. Chaos, in an art museum?
The complexity of the different sections of the building make it impossible to manually calculate the necessary dimensions of the various structures (the structures that will make sure that the building stays standing), and some machine power must be called in to help.
3D modelling
Using Frank Gehry’s hand-built models, measurements were transcribed into several packages and data solutions of the CATIA (Computer Aided Three-Dimensional Interactive Application) programme. Way back then, this was “a computer system […] which had only been used in the French aeronautical industry” explains Marta Arzak, Assistant Director for Education and Interpretation at the Guggenheim Bilbao Museum.
Although today programmes of this type are the norm in engineering and architecture studios (we now have BIM), at the time they marked a technological revolution which was frequently quoted by the media of the time as a huge novelty. AutoCAD, SolidWorks or ANSYS, to name but a few, are the ones used today, depending on the type of project.
Such was the novelty of this system that Gehry was at first reluctant to digitalise his project, but he was soon convinced when he experienced the ease with which it could be used and the results it produced, becoming a staunch supporter of this technology as the project progressed.
This programme uses calculation of finite elements, which was one of the first technologies to become popular for building purposes. Essentially, what it does is calculate point by point the tensions to which materials are subjected, generating a 3D model showing the different tensions (traction, compression, tension, bending, shear and torsion) and helping to calculate values for many of the museum’s structural elements: the steel structure, titanium cladding, plaster or glass, amongst others. It also helped to automate the cutting of materials such as stone.
This modelling includes several elements not usually considered as factors in construction, but which in a museum with large halls and high ceilings are of critical importance. Amongst others, the “wind” that the air within the building can generate, or the way in which sound is transmitted to make it pleasing to the ear.
The skeleton of an art museum
Once we have determined what the meccano must look like, it has to be put together. The 664 pilings mentioned earlier, which are 14 metres long on average, support a laminated steel frame which is in effect the museum’s skeleton.
Everything else rests on this frame, which is unique in that no two components are the same or symmetrical, with each of the parts having to be cut to size.
Though the structure may appear to be somewhat “deformed”, the fact is that it has been meticulously calculated, with no two joints being the same in the whole building. Hence the importance of the computer-aided design and calculations.
If the CATIA or similar tool had not been available at the time, calculations would have taken years, not only because of how complicated they were, but also because they had to be absolutely failproof, since other yet more complex structures (curved shapes, awkward location and weight) would have to be fixed onto this skeleton. So it is little wonder that this building has made it into the history books of construction.
We spoke with Juan Ramon Pérez – currently Building Director at Ferrovial, and at the time Head of Building in the Basque country and Works Manager for the Guggenheim Museum during its construction –, who answered a number of questions for us.
Interview with Juan Ramón Pérez, Works Manager for the Guggenheim Museum
The press at the time claimed (I imagine you read articles to this effect) that Frank Gehry’s handmade models “were a beautiful project, but altogether un-buildable”. And yet, you did it. You built a third Guggenheim, and it was a resounding success. What was the most complicated part of the process?
The Guggenheim Bilbao Museum is a building that was 20 years ahead of its time. Even today, when we’re celebrating its 20th anniversary, we could say that it is still 20 years ahead of the times.
Today, BIM (Building Information Modelling) is becoming the methodology to work with in architecture and engineering. It consists in channelling all the information of a particular project into a digital data model created by all the factors involved.
The Guggenheim Bilbao Museum was the first major project in the world to be built using BIM, so I guess that’s the answer to the question.
We were pioneers and innovators within the sector, which is both brilliant and complicated.
The rigid titanium panels that Gehry chose for cladding the building and which look rather like fish scales, don’t look easy to install. What did you do to make a rigid panel look alive?
Titanium was chosen after analysing many materials in detail for their resistance, physical, chemical and financial qualities: it is fantastically resistant to corrosion, long-lasting, very solid and with an incredible range of colours depending on the intensity and reflection of the light falling on it, which means that the colour changes all day long, from dawn to dusk.
The panels are very thin, just 0.38 mm, and this makes them look quilted rather than flat, and when the wind blows the whole building surface appears to flutter.
Something which is frequently overlooked in projects of this type is worker access. Was it particularly difficult to work on such a seemingly twisted frame?
It was indeed difficult, and financially incredibly costly.
All manner of lifting and support aids were used: elevator platforms, telescopic platforms, cranes… Climbers were also employed to provide rope access for certain areas and to perform specific tasks.
Inside, at some points of the building, special scaffolding was used which had to be adapted to all the different shapes and heights: close to 50 metres at the highest point (in the atrium).
If the main sculpture of the museum is the building itself, you could say that the second was the scaffolding that had to be put up. Only the first is permanent, the scaffolding was temporary.
Each part was unique, and in a meccano model full of unique pieces it is easy to mix them up. How do you monitor thousands of tonnes of metal to avoid errors?
The Guggenheim Bilbao Museum was projected in CATIA, a 3D design programme which was originally developed for the aeronautical industry. This programme represents each surface as an equation, which means that every single point on the surface is known.
For the building of all these parts, whether steel, stone, titanium or glass, machines were used which were numerically controlled with programmes linking in from the data provided by CATIA once the engineering part of the process had been established. Each piece could only be used in the specific place it had been designed for, and was uniquely identified by its coordinates, its thickness and it curvature.
In construction, we say very little about the importance of waterproofing. Was it difficult to insulate all these curved surfaces?
The outer skin consists of a base of galvanised steel covering the secondary structure (so basically tubular), and the waterproofing was applied to this. The titanium panels were then placed over this as the final layer.
The waterproofing layer is a high density polythene membrane which is flexible, self-adhesive, highly resistant to tearing, and self-healing. It is easy to work with and can be applied under a wide range of temperature conditions.
Access was the difficult part: depending on the area we were working on it was more or less complicated, and all the different lifting aids, as I said before, had to be used.
Any special story from the construction period you want to share?
In the days following completion of the project and its official opening, now 20 years ago, we used to say:
Much will be written and said about the Guggenheim Bilbao Museum in the future; we will simply be able to say that we built it.
And it makes Ferrovial and all of us who took part in the project immensely proud to be able to continue saying it.
And here’s a question I have to ask in view of the years gone by… What do you think of the building now, two decades on? Has it been able to adapt to new technologies? Is it in good architectural health?
Given that it was a building which was ahead of its time, and still is, its architectural health is great, and it is totally up to date in all the features that affect its operation and maintenance.
Suffice to say that the condition of the titanium panels is guaranteed to withstand the effects of the city’s pollution for 100 years.
The organic design on the outside, and transition from the frame
The skeleton or primary structure mentioned before has rectilinear components in the profiles used to put it together. However, both the outer and inner surfaces are curved, which added great complexity to the project.
The secondary structure (or horizontal curvature) and a tertiary structure (or vertical curvature, and ultimate expression of architectural complexity) are what provide the transition from hidden straight lines to the visible organic structure all visitors are now familiar with, both inside and outside the building.
All the fittings and machinery are hidden behind such complexity, as all the ducts and cabling for the various systems (irrigation, safety and security) usually condition the design.
The tertiary structure holds up a galvanised steel plate onto which the waterproofing layer (indispensable in a museum for obvious reasons) is adhered, as well as the thermal insulation and, as the final outer layer, the iconic titanium panels. This material, which brings the building to life and simulates bird feathers or fish scales, was chosen by Frank Gehry for its colour and the way in which it reflects the light.
Having said all this, not all parts of the building are curved. Large parts of the façade which is visible both from the river mouth and the city centre are straight, and finished off in limestone to create a contrast with the metal structures sitting amongst them.
The Guggenheim Museum Bilbao has become a benchmark for modern art, both as a museum housing important exhibits, and as an artwork in itself. It contributed to the transformation of a predominantly industrial city into Bilbao as we know it today, a city renowned for its culture, its art and its cuisine.
But, as we have seen, the building of this museum was not without its difficulties. And it also marked a turning point in architecture and building techniques and our understanding of construction methods. Today, 20 years after it first opened, the world continues to look to the Guggenheim.
Photos | Frank O. Gehry, Wikiarquitectura, Txemi López
There are no comments yet