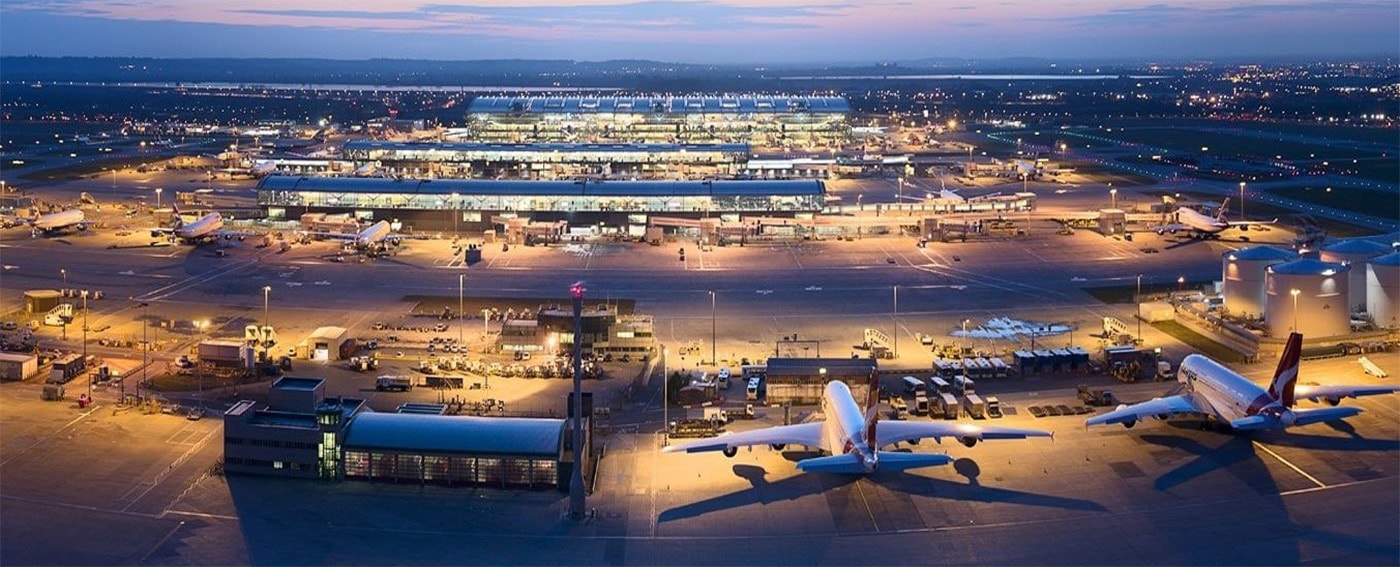
A project with clean energy: everything we stand to gain by committing to HVO fuel in Q6 construction at Heathrow
14 of June of 2021
Reducing carbon dioxide emissions on a construction site is always a challenge. There are multiple issues to address, different solutions to try out, and so many questions. At Heathrow, we’re faced with a major challenge when it comes to mitigating these emissions: we must meet the objectives set by the United Kingdom’s government, the airport itself, and last but not least, Ferrovial.
One of the most interesting solutions we’ve come across in recent years is using hydrotreated vegetable oil (HVO) as an alternative fuel to traditional diesel. HVO is a hydrobiodiesel from renewable resources; with it, we can reduce carbon dioxide (CO2) emissions from machinery by up to 90%.
Excavation as a testing ground
Using HVO in the Q6 construction at Heathrow Airport began with a preliminary study to determine exactly which of our activities was behind the most CO2 emissions. This study allowed us to verify that machinery was one of the main sources of emissions, so we could look for alternatives.
We decided to go with hydrotreated vegetable oil, an oil with chemical properties that are quite similar to diesel oil but come from a more sustainable source. It contains much less oxygen, so it produces fewer CO2 and nitrogen oxide (NOx) emissions and PM10 and PM2.5 particles when burned.
To understand its potential advantages and disadvantages, we tested it at the Ferrovial Construction Kilo Apron Substructure (KAD Substructure) project. The goal of this construction contract is to build a large underground area to connect terminals 2A and 2B. When completed, it will have the infrastructure to transport luggage and a fleet of trains to transfer passengers between the two areas. This large-scale site requires excavators, equipment to transport materials, and other machinery requiring a high amount of emissions.
To see how much they could be reduced, we compared the efficiency of a 17-ton HVO-powered excavator with a 22-ton diesel-powered one. We collected data on the fuel consumed, the hours worked, and the type of work performed to calculate and compare the carbon dioxide emissions that each emitted.
The results of our study were highly satisfactory. Using HVO in machinery like this can reduce carbon dioxide emissions by up to 90%, NOx emissions by 30%, PM10 by 75%, and PM2.5 by 84%. Another one of its main advantages is that it can be used in any engine.
For a broader perspective on the advantages of using it, we also wanted to get the operators’ opinions. According to them, the machines’ efficiency was not reduced, but their smoke emission levels were.
We also received information about a possible distadvantage: one of the subcontracted companies that provided us with the machinery told us that, according to a study, it is not recommended to use this oil in machinery that had previously used diesel. Although it is not proven, we decided that HVO would only be used in new machinery. We did so out of simple precaution to prevent any potential problems.
In addition to HVO and to ensure the maximum possible emission reduction, we also used electric and hybrid machinery on this project. This is where the task of finding and choosing the most efficient, powerful machinery, which is not always available on the market, comes into play. An example of this was the acquisition and implementation of 36-ton hybrid excavators for our project; only three or four of these are available in the United Kingdom.
The importance of not getting too comfortable
As is always the case when positive results are achieved, one of our actions was to share this success with the airport’s companies – knowledge sharing is one of Heathrow’s requirements for greater transparency and collaboration in reducing emissions – and with the rest of Ferrovial’s teams and divisions. This is the first project to date that has used HVO in machinery at Ferrovial, though its possible use for other projects is being studied.
These measures are of great importance at airports, where there is so much activity and such a high environmental impact. As a company, we have the responsibility to achieve the objectives set through alternatives and not to settle for simpler solutions. If it’s possible for us to test a solution that may be beneficial for the company on a construction site, we must take that step.
Our initiative for this Heathrow project also has a significant impact at the social level. In the United Kingdom, showing respect for the community and being more responsible with regard to our surroundings is highly valued. Along with our Health and Safety and Environment standards, this is why our project has been awarded the national Considerate Constructors Scheme (CCS) site award, one of the most prestigious recognitions in construction.
On a personal level, it is satisfying to be able to opt for solutions that are beneficial for society and the environment. At Heathrow, we have a huge advantage: we have a direct relationship with our engineers and project managers. When we find a possible innovation, there’s no problem trying it out.
Throughout my four years at Ferrovial, I have had the opportunity to participate in projects with hybrid and electrical machinery, equipment with renewable energy technologies, and many other solutions committed to sustainability. This one, which focuses on HVO, is just one more example of how we can commit to good practices and really change things.
There are no comments yet